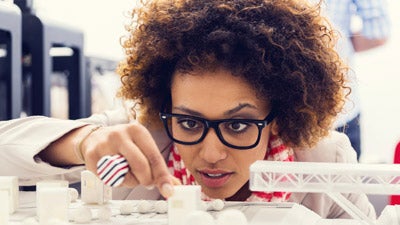
The global pandemic has caused a shift in our everyday lives that we never imagined possible. With so much indirect, yet fundamental change imposed on individuals, businesses and manufacturing operations, there has been a clear need for organizations to diversify and adapt.
So, what does this mean for the role of 3D large printing companies, and what lessons have we learned in light of the coronavirus?
3D printing in healthcare
3D printing has been used in the medical industry for decades, producing various items including implants, prosthetics, dental moulds, devices and anatomical models. However, with the new urgency to speed up processes to produce and deliver medical devices at a much faster rate, we have seen the technology modify to address different challenges related to the Covid-19.
CPAP machine case study
A recent 3D printing Covid 19 case study demonstrates specifically how on-demand manufacturing and rapid prototyping supported engineers and university clinicians in the making of CPAP devices for hospital patients within shortened time scales. Used to help remove the burden of dependence on ventilators, CPAP machines are able to keep a patient’s airways open and are less invasive than ventilators, therefore their production was invaluable in the fight against the Covid-19.
The manufacturing project was two-fold. Firstly, there was a requirement to create two new tools to make 10,000 brackets that hold devices next to a patient’s bed, and secondly, to develop a tool to make a cap preventing the entry of air to a device. Using 3D printing, four versions of the brackets were created quickly and easily to help ensure accuracy, and alterations were made for the cap, both of which speeded up the manufacturing process.
The fundamental challenge behind the project was to improve the development times for the tooling required to make the parts, and the injection moulding of the parts. Moving from prototyping to production was also crucial, with a time and motion study optimising the cycle time, and regulatory approval gained in just 14 days.
The importance of speed to market
In manufacturing as a whole, there has been a continued focus on the need to improve time to market and ultimately, to help manufacturers respond to changing consumer needs. 3D printing has already played a role in this with its rapid prototyping capabilities. However, due to the serious nature of a pandemic, the need for speed to market has forced more innovation to come to the fore. Let’s take a look at more of the specific changes that have been made.
Use of different materials
To help improve the times, some manufacturers have begun using different materials in the production of medical devices. For example, steel is traditionally used to produce moulds for injection moulding, however, using an alternative material like aluminium can accelerate the production process. Often, for bridge manufacturing, where volume requirements are lower, aluminium is an excellent alternative to steel. Parts can be produced within 15 days, unlike steel moulds which can take up to 12 weeks, and manufacturing costs are also lower. In addition, different types of materials have been used to print face shields, for instance, Polyactic Acid (PLA) which can be disinfected, therefore making them reusable and economical.
Use of machinery and software
Two of the most prevalent types of 3D printing technology used to produce medical devices are Stereolithography (SLA) and Fused Deposition Modelling (FDM). A one-step process from CAD design to printing, FDM parts can be ready in a matter of hours, sometimes minutes, depending on the complexity of the shape required. It is also a highly accurate method using heated thermoplastic filament which produces accuracy of .005 inches – a necessity when it comes to the production of medical devices.
Similarly, SLA printing also produces high precision parts thanks to the fineness of each layer produced in the 3D printing process. Parts can be produced in a matter of days and costs are reasonable. In addition, optimising the use of CAD software also supports the speed of processes which, after the prototyping stage, can perform an analysis for manufacturability.
Final thoughts
The pandemic has seen resources all over the world pushed to the maximum, but in response, the 3D printing community has come together to tackle this through improving the pace of production. By adapting to more on-demand manufacturing via a number of different routes, the course of 3D printing has potentially changed for good and indeed, for supply chain operations across the world.
2045 Views