3 Ways to Ease into Industrialized Construction (It Pays to Be Diligent)
By: Redshift
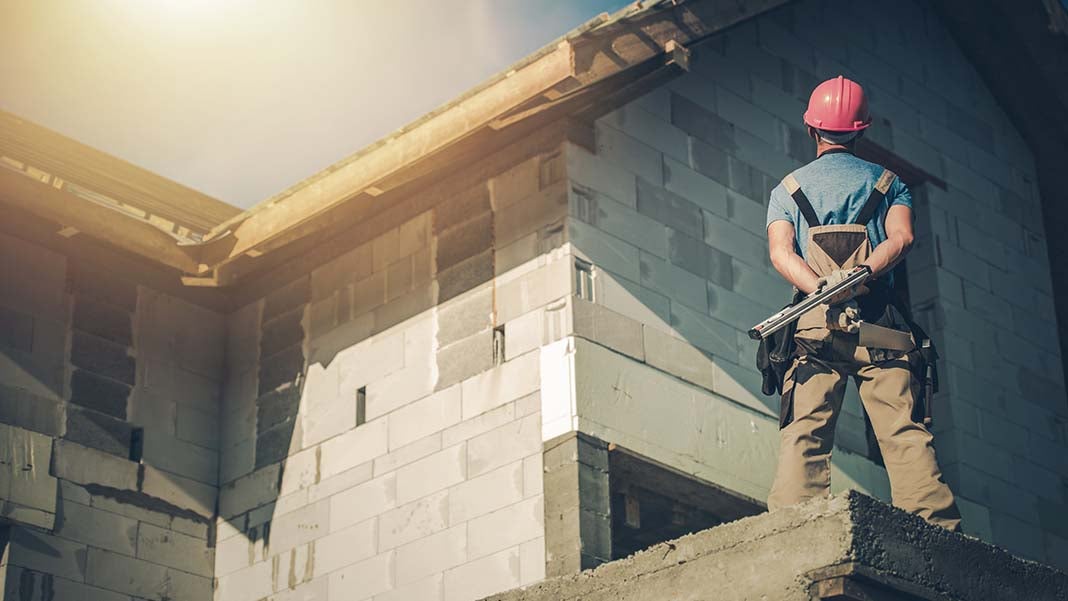
“Industrialized” construction may not exactly sound fun to longtime contractors and builders who relish the craft aspects of their trade. But the adoption of industrial, prefabricated, and manufacturing techniques by construction firms is an emerging way to realize the efficiency gains so elusive in architecture, engineering, and construction while improving profitability, project quality, and even addressing skilled labor shortages.
“Implementing industrial techniques in our supply chain and field work is so important from quality-control, safety, and scheduling points of view,” says Todd McCabe, vice president of project services at Consigli Construction Company. “Plus, here in Boston, we are really struggling to meet the demand for skilled labor on projects; the workforce is aging out. So the more we can move prefabrication work to controlled environments, the more we’re able to reduce that pressure.”
Consigli, working with ManufactOn—an Autodesk Forge Fund partner founded to help the construction industry integrate prefabrication tools for supply chain, prefab production, and planning—has prioritized the industrialization of its construction business for several years. But it isn’t a transition it has tried to implement at breakneck speed. Rather, Consigli found that a gradual transition that focuses on individual processes worked best.
Here are three ways Consigli moved gradually into industrialized construction.
1. Take a Close Look at the Construction Supply Chain
In large-scale commercial construction, managing vendors and supplies is as complex as managing supply chains at manufacturing plants—maybe more complex, as construction supplies and materials change with each new project and might need direct delivery to project sites, prefabrication facilities, or a central warehouse. Better supply-chain management is also low-hanging fruit when it comes to saving money and spotting opportunities for part-kitting and off-site prefabrication.
“When I started here 20 years ago, we were using whiteboards and magnets to manage supplies, and we thought that was pretty sophisticated,” McCabe says. “But in retrospect, some supplies were absolutely getting lost, or wasted on-site, and we had a lot of loose material in uncontrolled environments. It was inefficient to say the least.”
Now, having implemented the ManufactOn material-management module, Consigli is using QR codes and mobile devices to track and coordinate deliveries and apply industrial warehouse–management techniques for much greater visibility into the entire supply chain.
2. Look for Opportunities to “Kit” Supplies and Prefabricate Modules
One of Consigli’s goals was to increase the percentage of just-in-time deliveries to jobsites, which minimizes congestion on crowded projects and is more efficient. One approach is working directly with vendors to improve deliveries. For example, Consigli now receives doors and door hardware as kits rather than as individual loose items.
Traditional construction depends heavily on skilled labor on jobsites, as basic materials and parts are assembled into completed facilities. Industrialized construction aims to move much of this skilled work off-site, into controlled environments. This can be done by kitting parts off-site, or by actually prefabricating large modules at dedicated facilities.
For example, Consigli now takes advantage of better supply-chain insight by packaging all the materials needed to install and finish windows at its warehouses, rather than shipping them separately to projects. Warehouse workers collect the windows, trim, drywall, and fasteners into material packages, then deliver them in wheeled Consigli “smart carts.” On-site workers wheel the carts to the rooms they’re working on and have everything they need in one place, without extra materials getting in the way.
Consigli uses 3D modeling tools such as Autodesk Revit to create models of individual floors, rooms, and smaller components like electrical and plumbing modules. These are used as guides for precise off-site prefabrication; large modules can then be delivered to jobsites, ideally on the day they’re needed. To continually improve deliveries and prefabrication, Consigli depends on short end-of-day meetings to get feedback on kit completeness and module fit.
3. Empower a “Self-Perform” Team to Do More Prefabrication and Kitting
Consigli maintains an entire “self-perform” division, known as Riggs, which functions as a separate, multitalented subcontractor that can be plugged in as needed on projects. “Riggs’ sole customer is Consigli, and it’s like having a subcontractor available that has the same values as our company,” McCabe says. “They’re able to do sitework, rough and finish carpentry, masonry, doors, and windows—and anything else we need done—with all the attention to safety and quality that we expect from ourselves.”
Now, kitting and prefabrication are considered a subcontracting specialty that Riggs can perform on Consigli’s behalf. A recent academic facility project is a good example. “This project includes a complex sunshade system with many parts, and normally we would just assemble that on-site,” McCabe says. “We asked Riggs to find ways to kit and prefabricate the parts off-site.”
Riggs crews looked at the problem and found that many of the sunshade components could be packaged together, with the correct fasteners and hardware attached to frame pieces. And many components could actually be assembled into relatively large modules, reducing on-site construction time and congestion. “We’re certainly going to look for even more ways to do that,” McCabe says.
Dedicating internal crews to industrializing construction processes has been a big win for Consigli. By doing the work of identifying and completing prefabrication opportunities, the company has good data on the benefits and is able to collect feedback that continues to improve the whole process. So, even though the move to industrialized construction has been gradual, it has been steady, with efficiency gains at every step along the way.