How Lean Construction Empowers the Front Line for Better Teamwork
By: Redshift
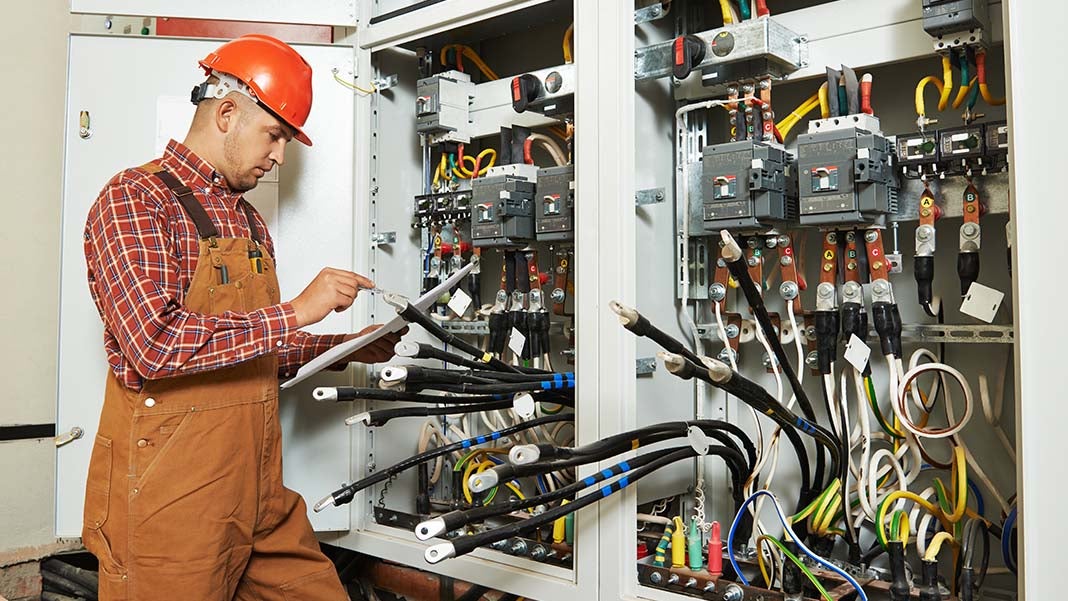
A command-and-control hierarchy used to be the only way to get things done before the 21st century. Your superior gave you a command, and you said “Yes, sir”—or paid the price. But what if the command didn’t make sense in practice? What if it was outdated or inappropriate? You still had to obey.
Things are different now. Now, you have what authors David Alberts and Richard Hayes call power to the edge, in which the command chain crumbles and the people doing the work are empowered to make decisions that make sense in real time. This is a movement that has emerged in the military, and it parallels a “new” construction movement—it’s over 25 years old already—called Lean Construction.
Power to the Front Line
In 2004, U.S. General Stanley McChrystal was shocked at how the formidable forces under his command were losing against the ragtag, seemingly disorganized, and ill-equipped Al-Qaeda in Iraq. Operating in small self-organized and self-synchronized groups, Al-Qaeda didn’t have a central authority meting out orders. It had a shared mission and a general alignment with the mission, but each localized group was left to its own devices to forward that mission. That made Al-Qaeda agile, flexible, adaptable, and hard to beat. McChrystal responded by turning the traditional military hierarchy on its head.
“We had to tear down familiar organizational structures and rebuild them along completely different lines, swapping our sturdy architecture for organic fluidity, because it was the only way to confront a rising tide of complex threats,” he writes in Team of Teams: New Rules of Engagement for a Complex World. “Specifically, we restructured our force from the ground up on principles of extremely transparent information sharing (what we called ‘shared consciousness’) and decentralized decision-making authority (‘empowered execution’).”
Power to the Crew
Lean Construction evolved on the same principles. It began when co-founders of the Lean Construction Institute, Greg Howell and Glenn Ballard, were trying to figure out how to improve performance on construction projects. Ballard had the idea of measuring performance against the weekly work plan.
“We have since found that, all over the world, only 50 percent of the tasks assigned by the foreman are fully completed in the week promised,” Howell says. Instead of blaming the workers, Ballard and Howell asked what was standing in the way of completing the tasks. Answers varied anywhere from “the materials weren’t available on time” to “this other crew was in the way” to “the drawings were wrong.”
It became clear that completing tasks on the weekly plan would depend on a number of factors: materials, information, tools, space to work, and completion of previous activities. “We found the only way to improve performance was for crews to decline assignments when impossible to deliver,” Howell says. “In lean manufacturing, the duty of workers is to stop the line rather than let a defect move forward. So we redefined the weekly plan: Assignments made by a foreman are promises to the following crew.”
“An order is a request with sanctions; if you don’t do it, you’re in trouble,” recalls Howell, who served as a member of the Seabees—part of the U.S. Naval Construction Forces—in Thailand and Vietnam. Once you replace orders with promises by the people closest to the work, you see a radical shift. According to Howell, that shift was responsible for weekly work-plan performance shooting up to 75 percent and even 90 percent.
Power from Shared Information
Alberts and Hayes, authors of Power to the Edge: Command and Control in the Information Age, say that traditional organizational models “prize deconfliction over synergy.” Deconfliction is avoiding conflict. In Henry Ford’s assembly line, Ford divided the labor by specific steps and tasks. For example, he separated the metal workers from the rubber workers to avoid conflict between them.
But the power-to-the-edge military model and Lean Construction espouse synergy instead. In that scenario, metal workers and rubber workers (or electricians and plumbers, as the case may be in construction) find synergies in their work. Instead of maximizing their own piece of the puzzle, they work together to maximize the entire project.
Related Article: Can You Change the Culture?
Both the power-to-the-edge military model and Lean Construction seek to break down silos through shared information, rather than hoard information and knowledge at the top of the hierarchy or between groups. “Imagine a project where the foreman has an iPad: It gives him tremendous information and insight into everything about the project,” Howell says. “Does he then need to run everything by his superintendent?”
In the traditional military organization, only the top brass were privy to all of the information; orders were given along with need-to-know information. But in the power-to-the-edge model, information is made readily available to everyone. “We looked at the behaviors of our smallest units and found ways to extend them to an organization of thousands, spread across three continents,” McChrystal says in Team of Teams. “We became what we called ‘a team of teams’: a large command that captured, at scale, the trains of agility normally limited to small teams.”
It’s clear that the information age has facilitated a deep transformation in huge institutions such as the military and construction industry. But it is only a part of the fundamental paradigm shift that pushes power from the top to the edge, where the work actually happens. Howell believes it is a move in the right direction: “We will be best as a community when we bring power to the edge.”