The Essential Guide to Balancing Speed and Quality in Operations
By: SmallBizClub
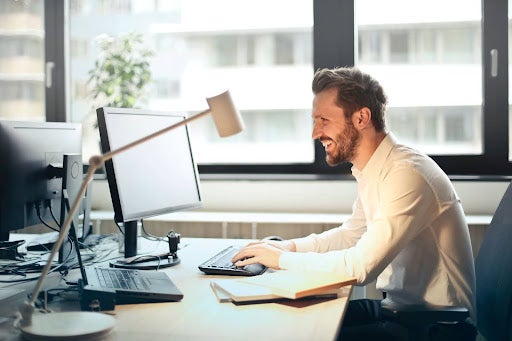
In the modern business landscape, a crucial determinant of success is the ability to balance speed and quality in operations. This equilibrium is vital, as it dictates a company’s efficiency, customer satisfaction, and overall market competitiveness. Navigating this balance, however, is a complex task that involves strategic planning and continuous improvement.
Understanding the Speed-Quality Trade-off
The speed-quality trade-off has been a long-standing challenge in operations management. Traditionally, an increase in production speed often came at the cost of lower quality, and vice versa. However, in today’s customer-centric market, businesses must deliver high-quality products and services rapidly and consistently. This challenge intensifies in industries like healthcare and aviation, where quality is non-negotiable, regardless of the demand for speed.
Strategies for Speed Optimization
Process Automation: In sectors like manufacturing, automation has revolutionized speed. For example, in automotive manufacturing, robotic assembly lines perform tasks with precision and speed unattainable by human workers, massively reducing production time while enhancing consistency.
Lean Management Principles: Lean management focuses on eliminating non-value-adding activities (‘waste’). In service industries like banking or insurance, this might involve digitizing paper-based processes, thus speeding up customer service without compromising accuracy or compliance.
Technology Integration: The integration of advanced technology, such as AI and machine learning, can exponentially increase operational speed. In logistics, for example, AI algorithms optimize route planning, leading to faster delivery times while reducing fuel consumption and costs.
Ensuring Quality While Maintaining Speed
Quality Control Systems: Effective quality control is key to maintaining standards. In the food industry, for example, quality control systems ensure that, despite the speed of production, food safety and hygiene standards are never compromised.
Employee Training and Engagement: Investing in employee training is crucial. In retail, well-trained staff can handle customer inquiries swiftly and accurately, enhancing both service speed and quality.
Continuous Improvement Approach: Adopting continuous improvement methodologies like Kaizen or Six Sigma helps businesses refine their processes. In software development, this might involve iterative testing and development cycles, allowing for rapid bug fixes and feature improvements without sacrificing product quality.
Case Studies and Real-World Examples
Manufacturing Automation: Toyota’s implementation of automated assembly lines and the Just-In-Time system revolutionized automotive manufacturing, significantly reducing lead times while maintaining the highest quality standards.
Lean Management in Services: Financial institutions like Bank of America have employed lean techniques to streamline their operations, reducing process times for loan approvals while maintaining rigorous compliance checks.
Continuous Improvement in Tech: Tech giants like Google continually implement iterative development processes in their software solutions, enabling quick rollouts of new features with a stringent quality assurance process.
Balancing Speed and Quality in a Digital Age
The digital age has introduced tools and methodologies that help balance speed and quality. Big Data and advanced analytics enable companies to predict and preemptively address potential delays and quality issues. For example, in e-commerce, data analytics can predict high-demand periods, allowing companies to scale up operations rapidly without affecting the order fulfillment quality.
Emerging technologies like the Internet of Things (IoT) offer further advancements. In industries like manufacturing, IoT devices can monitor equipment performance in real-time, flagging any potential quality issues instantly and reducing downtime.
Conclusion
Achieving a balance between speed and quality in operations is a dynamic and ongoing process. It requires a mindset that values precision and efficiency equally, supported by a culture of continuous improvement and innovation.
Businesses must stay abreast of technological advancements and evolving best practices to maintain this balance. By doing so, they can not only satisfy but exceed customer expectations, securing a competitive edge in their respective markets. In essence, the fusion of speed and quality in operations is not just a strategic goal; it’s a fundamental requirement for sustainable business success in the modern era.
2098 Views