How Can Robots Improve Electronics Manufacturing?
By: Emily Newton
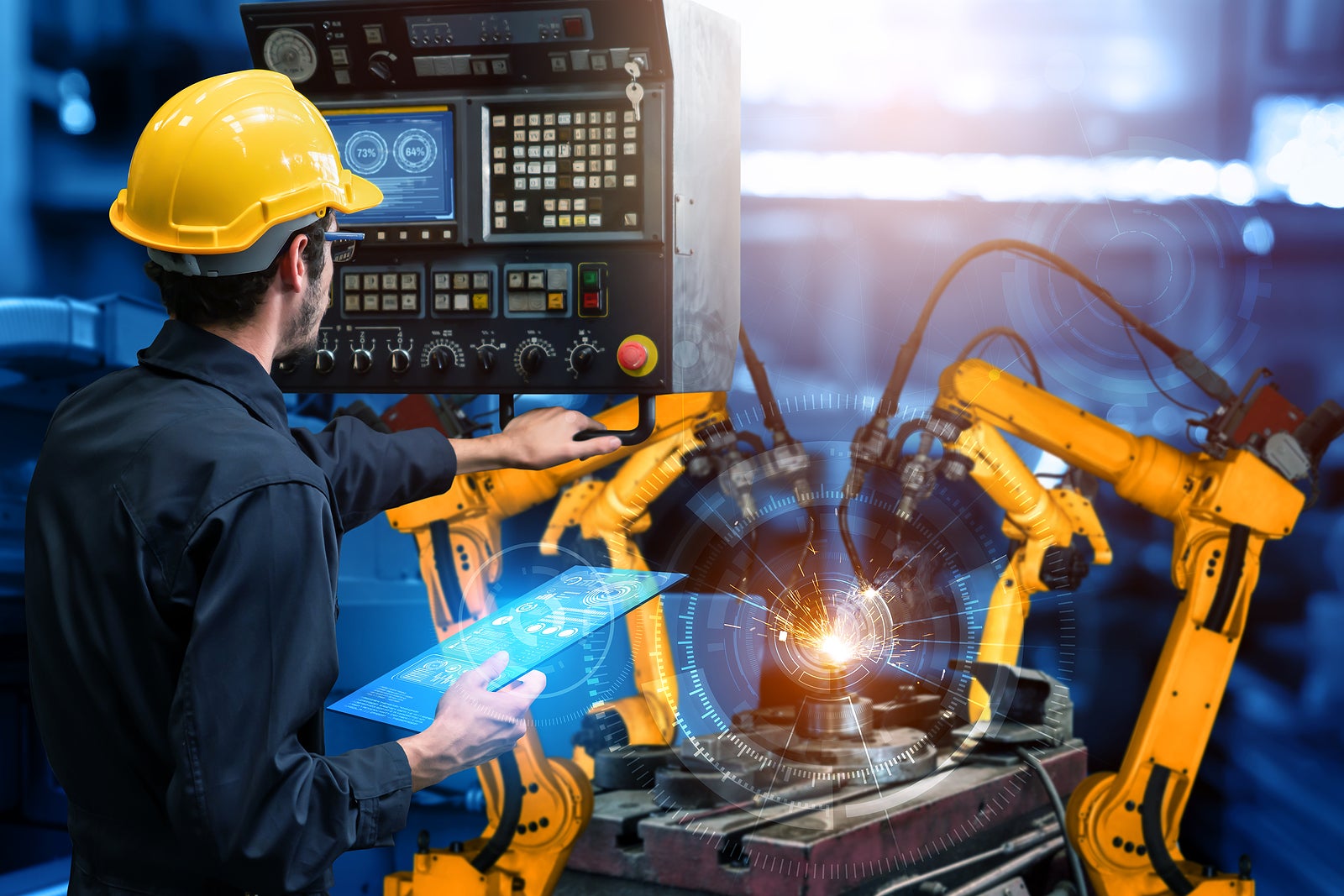
Modern electronics manufacturing faces a range of challenges — increased complexity of parts, major growth in demand, and continuing miniaturization — that have made precision and speed more critical than ever for the industry.
Human workers alone can’t handle the demands of modern electronics manufacturing, making robotics essential to factory workflows.
The rise of Industry 4.0 tech has had a major impact across manufacturing. New manufacturing robotics leverages artificial intelligence (AI) and related technology to be more autonomous than their predecessors or work in close proximity to human workers.
Soon, these robots have the potential to reshape how manufacturers across the electronics industry approach work.
Industrial Robots and Process Automation
The increased precision, speed, and consistent performance of modern robotics have made it possible for electronics manufacturers to significantly increase factory throughput.
Industrial robots, which can entirely automate a particular task or workflow, both speed up existing manufacturing processes and free skilled workers for tasks that cannot be automated.
Common applications of industrial robotics in the electronics industry include packaging, palletizing, gluing, sealing, measuring, inspecting, and assembly — often in the form of screwdriving or part insertion.
One area where industrial robots and process automation has been especially valuable is in testing. Because effective testing is so essential to quality assurance in electronics, finding ways to streamline testing allows for greater efficiency in the overall manufacturing process.
In some cases, automation can also help pave the way for new technology that helps manufacturers handle emerging testing challenges.
For example, the auto industry is increasingly dependent on monolithic electronic sensors that create multiple outputs — like position sensors that provide dual outputs, eliminating the need for extra sensors in some applications.
Sensors with a single output can be easily tested with common test circuit interfaces, but sensors that produce multiple outputs may require different hardware.
The development of new, custom test circuit interfaces capable of testing these multi-output sensors ensures that the electronics industry will be able to continue testing sensors without having to depend on more manual solutions.
“Cobots” and Collaborative Automation
One major recent development in robotics has been the growing focus on human-robot interactions and collaboration. Rather than fully automate a workflow or task, new robots often prioritize flexibility and upgrades that enable them to work in close proximity with humans.
These collaborative robots, or “cobots,” are outfitted with safety features — like lightweight frames, force limiters, and padding on sharp joints — that make it easier and safer for human workers to work around them.
Cobots help workers manage tasks and processes that can’t be fully automated or must be completed in close proximity to humans — including machine tending, welding, and testing. Cobots often do not automate work, but instead reduce some of the burdens by simplifying repetitive tasks or providing support to human workers.
In practice, collaborative automation can help improve worker productivity, boost morale, and reduce the risk of musculoskeletal injuries, which can be caused by repetitive movements that manufacturing demands.
In electronics manufacturing, collaborative automation has become increasingly valuable as a flexible and multi-purpose solution to automating high-precision tasks like assembly, materials handling, insertion, dispensing, and labeling.
Because collaborative robotics are lightweight and designed to be quickly programmed or reprogrammed by operators, they can be moved and adapted to new workflows or tasks as needed.
This makes them a good fit for the electronics manufacturing industry, which faces both a growing labor shortage and major growth in demand for essential components. Greater flexibility in workflows enables manufacturers to both free up skilled workers as needed and adopt more agile responses to shifting demand.
Autonomous Warehouse Robotics
The movement of goods in and around the factory requires significant labor — typically in the form of dedicated employees who operate forklifts or move goods by hand.
New robotics are helping to reduce the labor necessary to move goods around the factory, without requiring significant alterations to facility layout.
Some electronics manufacturers use autonomous guided vehicles (AGVs) — track-bound robots that either use tracks or follow a predetermined path around the factory.
AGVs occur in different sizes and configurations. They’re used for a few different applications — including inventory transport, picking, and sorting. Standard-sized AGVs are similar to forklifts in size, weight, and function, and are typically used to move pallets or other heavy items around the warehouse with minimal human supervision.
Smaller robots may handle tasks like moving racks of small containers.
More advanced robots, called autonomous mobile robots (AMRs), are able to navigate without the help of a predetermined path of tracks, enabling more flexible use by factory owners.
These AMRs use AI-based machine vision and maps of the factory floor to navigate safely. Information from a front-facing camera, for example, can be analyzed by the AI algorithm to identify navigable floor space, workers, and potential floor obstacles. Data like floor plans can provide additional guidance and prevent potential accidents.
The same technology may be used by robots to identify labels on goods. This can enable a picking robot to select the right item to be transported without a human operator needing to specify which item or pallet to select.
Like industrial and collaborative robotics, these robots help free up workers from repetitive or dull tasks for more important work.
Using Robots to Streamline Electronics Manufacturing
Faced with a growing labor gap, volatile demand, and supply chain instability, electronics manufacturers have turned to robots to streamline factory operations.
In electronics manufacturing, new robotics can be used to fully automate work or provide extra assistance to human workers. The rise of more sophisticated warehouse robotics is also improving factory throughput by making it easier to transport goods around manufacturing facilities.
1920 Views