5 Reasons Why Manufacturing Businesses Should Use an MRP System
By: Anees Saddiq
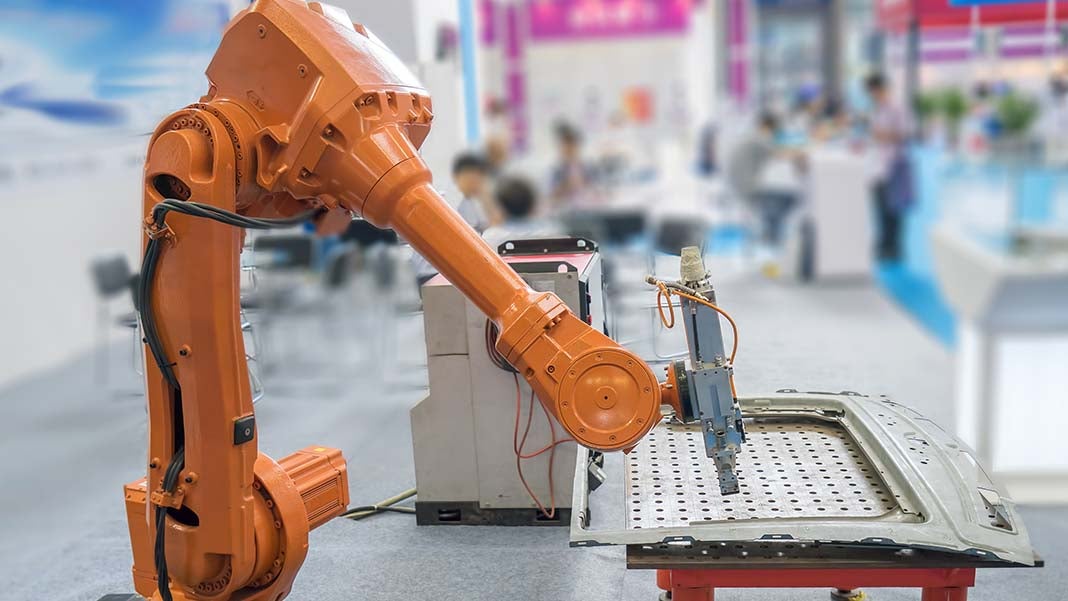
MRP (or material requirements planning) systems calculate raw materials, sub-assemblies, and components needed to manufacture a product. They enable efficient scheduling, production planning, and inventory control to streamline manufacturing processes. A good MRP software essentially minimizes lead times and maximizes service levels to boost business efficiency, following three steps:
- Tracking raw materials and components on hand
- Understanding low inventory that needs reordering
- Scheduling the production or purchasing of raw materials
This article discusses the reasons why MRP systems are important for manufacturers and how they can improve a business’ productivity.
1. Inventory control from raw materials to finished goods
Inventory management plays a significant role in achieving manufacturing efficiency. MRP systems help you understand exactly how much inventory you need to meet your customers’ demand, reducing the inventory carrying costs. You keep track of inventory from raw materials to finished goods, create reorder points, and avoid stock-outs.
2. Master production planning
MRP systems identify bottlenecks in the production line caused by lack of material. The system automatically reroutes production or recommends production of a different product where materials are available. This means that manufacturers can plan their production lines, despite material availability constraints. A master production schedule (MPS) is the big-picture plan to evaluate the production of your finished goods. It contains details on s how much needs to be produced in a specified period of time. It is the backbone of your manufacturing business helping you adjust production based on demand, avoid stockouts, improve efficiency and reduce costs.
3. Resource management
Raw materials are essential in any manufacturing process. An MRP system offers information on raw materials’ availability and expected yield and helps manufacturers clearly understand what resources to engage in the process. It also provides details on what equipment is required and when, if extra labour is needed, and whether to hire or buy operational assets.
4. Data management
Analysing, understanding, and presenting data in visually appealing formats is necessary to improve the decision making processes. MRP systems handle this information, through processing and documenting purchasing, inventory, deliveries, and cash flow data into receipts, invoices, lists, reports, or documents.
5. Time-saving
The automation offered by MRP systems means that little human intervention is necessary to manage inventory, purchases, and production. The accuracy these systems provide outruns any error-prone human method. They also manage and store production data, which eliminates the need for specific human resources attributed to these functions.
Concluding thoughts
An MRP system helps to effectively manage inventory, schedule production, and purchase raw materials. It helps to avoid overstocking or stock-outs and ensure high quality standards through traceability. You cut costs, mitigate waste, and improve your overall processes. With full visibility into your manufacturing, you can spend this extra time doing what really matters: growing your business and refining your products to satisfy customers’ demand.
3003 Views