5 Considerations for Purchasing a PLC for Your Facility
By: Dan Coconate
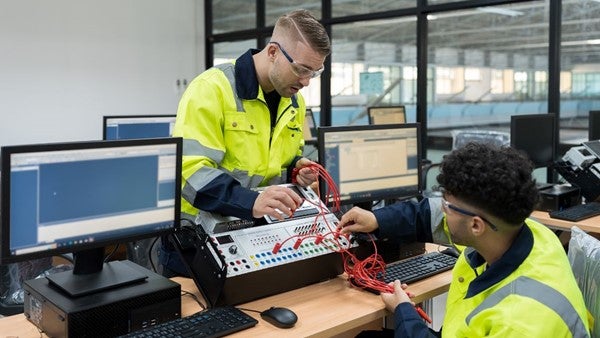
Are you in the process of upgrading your facility with a programmable logic controller (PLC)? These powerful devices can revolutionize your production line by optimizing control systems and streamlining operations. But with so many options on the market, it’s essential to choose the right one for your specific needs. Explore some of the critical considerations you, as a business manager, should keep in mind when purchasing a PLC for your facility.
Compatibility With Existing Systems
Before purchasing a PLC, you must ensure that it’s fully compatible with the existing systems and equipment in your facility. This means thinking about the communication protocols, input/output modules, and other components the PLC needs to interact successfully. If the new PLC fails to integrate seamlessly into your current operations, it can lead to increased downtime and a reduced return on the investment.
Scalability and Expansion Options
As you expand your system’s capabilities, it becomes necessary to enhance the PLC device to meet those new demands. When selecting a PLC, make sure it offers the scalability and modular design required to accommodate your facility’s future growth. This could mean choosing a PLC that supports additional input/output modules or memory expansion, ensuring that the system can effectively manage an increasing number of processes and equipment.
Budget and Maintenance Costs
It’s also important to strike a balance between the initial investment and the long-term costs associated with using a PLC. High-end PLCs may offer advanced features and increased flexibility, but they often require a larger upfront investment. Business managers should consider the maintenance costs involved and weigh them against the benefits provided by the specific PLC. Sometimes, a more affordable PLC that meets your facility’s requirements could prove to be a more viable option.
Chosen Programming Language
The programming language used to develop the PLC’s software is an essential factor in your purchasing decision. Common programming languages for PLCs include Ladder Logic, Structured Text, and Function Block Diagram. Your choice of programming language can significantly influence the type of PLC you buy. For example, if your facility’s engineers are familiar with Ladder Logic, it would be more beneficial to purchase a PLC that supports this programming language. By choosing a programming language that best aligns with your facility’s expertise, you can reduce training costs and increase efficiency during the implementation phase.
Manufacturer Support and Training
Another vital consideration for purchasing a PLC for your facility is how the manufacturer can support your operations team following the sale. Choose a PLC from a reputable manufacturer that offers comprehensive technical support and training. This will help ensure a smooth transition to the new system, allowing your team to troubleshoot efficiently and prevent any potential operational hiccups during the PLC’s deployment.
Selecting the right PLC for your facility involves carefully assessing several factors. By considering each of these aspects and making an informed decision, you can enhance the overall efficiency of your facility’s processes and contribute to your business’s long-term success. Put in the work today for a faster, more productive tomorrow.
1182 Views