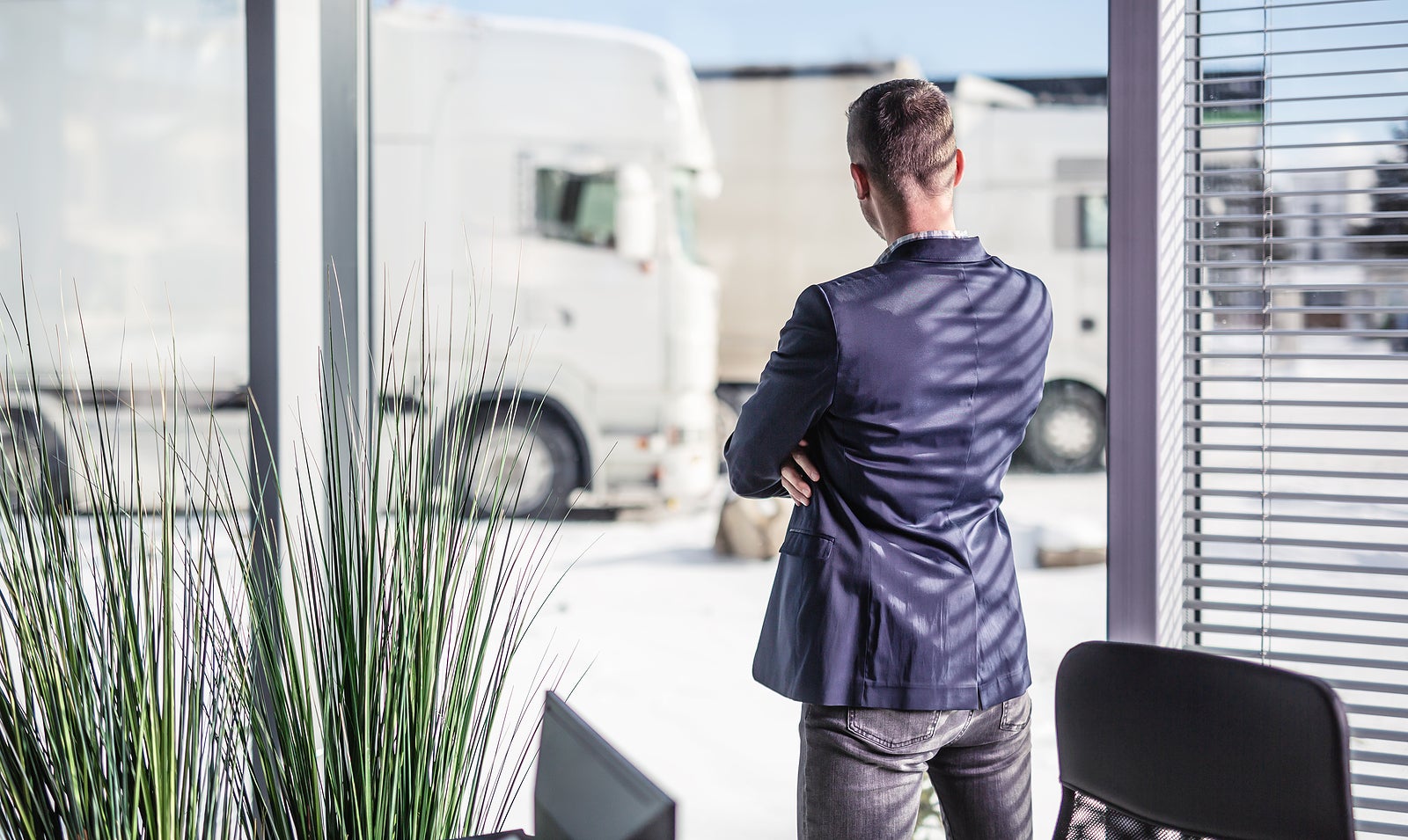
The efficiency of your work fleet can make a difference in how many vehicles you have and ongoing costs associated with sending technicians out on jobs. Improving your fleet’s management workflow isn’t difficult but does require some attention to detail and study of your current systems.
From fleet service management to ensuring your vehicles comply with local regulations requires organization. Collaborating with your team in real time and utilizing available software ensures you never miss a beat and work at optimum levels.
How Can Fleet Management Be Improved?
According to Automotive Fleet Magazine, approximately 3.2 million commercial fleet vehicles are in service, not including government and rental companies. You would think companies would have the perfect systems in place for smooth workflow. The problem is that every business operates a little differently, so finding your perfect processes requires time and dedication.
Although any workflow schedule must be tweaked to match your company’s goals and needs, there are some things you can do to immediately improve your fleet management workflow.
1. Inventory Your Assets
Before you can create a smoother process, you must understand where your assets are and how effectively you’re currently using them. Do a complete audit that looks at all your fleet vehicles, statistics on how often you’re maintaining them and repair costs and inventory of your personnel and how effectively you’re utilizing their time and skills.
As you complete your audit, make note of any areas you feel need improvement. Put a star by the ones you want to revisit or highlight them for further study.
2. Invest in Fleet Management Software
Fleet management software can complete in minutes what it would take you months to figure out. You can see where time gets wasted or if you send techs on jobs that are on opposite sides of town. It’s much better to send your techs out in a circular pattern so as not to create trips back and forth across town, which wastes time and effort.
Seek a fleet management software solution with Locate2U with real-time tracking and cloud-based services. You want to know where your fleet is at all times so you can better see how to tweak routes and where time and effort gets wasted.
3. Pay Attention to Traffic Patterns
Study your area traffic patterns. Can you dispatch service techs at a different time so as to avoid rush hour traffic or bottlenecks? Traffic patterns can waste a lot of your service technicians’ time if you live in an area prone to them, such as a big city.
Take note of where your fleet gets stuck in traffic or construction and seek new routes or better scheduling to avoid the issue. For example, you could book jobs in the morning near your office, so it doesn’t take long to get there.
Once rush hour passes, move technicians to other areas and then back close again toward the time everyone gets off work and traffic picks up.
4. Set Safety Standards
Businesses everywhere are having a hard time filling open positions with the current employee shortage. Setting safety standards protects your skilled technicians and prevents a situation where half your workforce is out with injury or illness.
It’s almost impossible to improve your workflow if you don’t have enough people to cover the work. If you need more technicians, hire them. You may have to pay a bit more or offer perks to attract them away from your competitors, but the result will be higher customer satisfaction and word-of-mouth referrals.
5. Add Sensors
With the addition of 5G technology, putting as much information as possible while on a job run is easier than ever before. You can automate much of the work and use the data and reports to improve workflow and fix issues within your system.
The Internet of Things (IoT) taps into cloud technology and all types of wireless devices to connect different fleet vehicles and workers. Experts estimate around 152,200 new IoT devices will connect to the internet every minute by 2025.
Embedding sensors into your fleet vehicles allows automated reporting back to whatever software you choose. You can get reports on where the vehicles spend the most time, maps of routes and alerts if something needs maintenance before it becomes a costly repair.
6. Automate Data Entry
Fleet managers spend a lot of time entering data from drivers and keeping track of reports. What if you could automate much of that work and spend the time instead on checking vehicles, tire pressure and training your technicians?
Provide your workers with a mobile device so they can check off things as they complete them. You can also speed up their workflow process by having a one-click option to check off completed work. They can still enter notes when needed, but for most jobs, they can just check off boxes to show what work was completed and then move on to the next task.
7. Talk to Your Staff
Your field techs are out in the real world every day and likely have a lot of ideas about how to fix any issues you may run into with workflow. Allow an anonymous suggestion program for those who worry about speaking up on issues. Have an open-door policy so your staff feels comfortable coming to you and making recommendations on how to fix problems.
The more you understand about the way your fleet management works, the better you’ll be able to fix any issues as they arise. A little bit of attention to detail and utilizing current technology goes a long way toward creating a highly productive fleet and technician team.
3167 Views