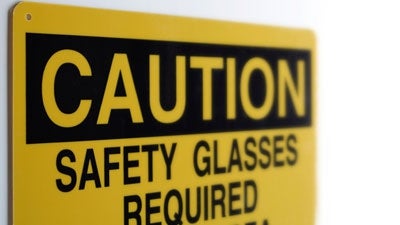
Creating a safety program for your workplace can be an overwhelming task. It can seem like there are innumerable ways employees can hurt themselves—and just as many OSHA regulations to prevent injuries from happening. Where do you start and how do you know where to go?
Author: Emma Sturgis is a freelance writer living in Boston, MA. She writes most often on small business and education.
Start with What Is Already Known
If you are starting a safety program from scratch, address the most serious workplace hazards first and work down to the least serious. Get a complete list of accidents in the past ten years from your risk manager and study it, noting which departments have had employee hospitalizations and or injuries with days away from work. Those departments or jobs deserve your attention first.
Maintenance and Machinery Always Need Safety Programs
After reviewing your company’s accident record, review its operations. If your company does any manufacturing using machinery, there will likely be safety issues with machine operators keeping their fingers, hands and other extremities safe around moving machine parts. If your company has maintenance employees who work on machinery, equipment or building systems, there will almost certainly be significant safety issues for them, too.
Identify the Moderate and Low Hazard Tasks
Once you’ve cataloged past injuries and accidents and identified areas of machinery and maintenance safety, review the remaining departments for potential safety issues. Back strains, lacerations, slips and falls and ergonomic problems are all typical injuries for lower-hazard areas of a business. Examine your company’s history of emergency management—when disaster struck, did everyone follow procedure without hesitation? A specialist from Arpel Security Systems, a security company in Vancouver, recommends that business leaders review all basic emergency procedures with their employees on a regular basis. This will help employees have a better understanding of their role in the event of an emergency.
Research OSHA Requirements
After identifying the most serious safety issues, identify the bare safety minimum requirements to make those jobs safe. Using OSHA regulations as the bare minimum safety requirement provides a two-fold benefit: Focusing on OSHA compliance gives your new safety program a place to start and it helps you in case you get an OSHA inspection. Go to OSHA’s webpage and determine if your state has its own plan or if federal OSHA has jurisdiction in your state. Using what you’ve learned about your company’s safety issues and whether your state has its own plan or relies on federal OSHA to enforce workplace regulations, research the regulations to determine what’s required.
Related Article: 5 Important OSHA Regulations You Can’t Ignore
Once safety priorities are identified, build relationships with your production and maintenance management to get their buy-in on safety efforts in their departments. OSHA’s website and your worker’s compensation insurance company offer training materials and other resources. Being the safety person in your workplace can be difficult, but it is a rewarding job to keep your co-workers safe.
Published: December 23, 2014
3514 Views
3514 Views