3 Keys to Safe, Efficient Materials Storage and Inventory Management
By: Hellen McAdams
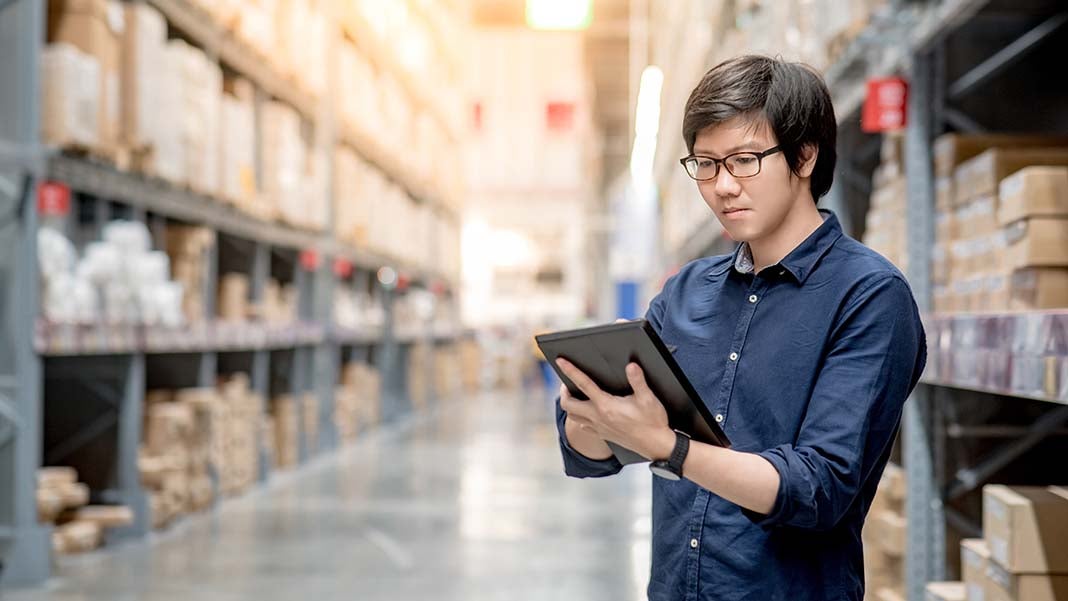
Improper storage of materials had deadly consequences for one worker when an explosion rocked a construction site off U.S. 280 in Harpersville, Alabama. Christopher Anderson of Mississippi was killed when he opened a storage container containing flammable materials while installing natural gas lines. Four other workers were injured, passing vehicles and a nearby road were damaged, and the roadway had to be shut down.
Liquefied petroleum gas tanks and oxygen and acetylene cylinders had been stored in unventilated Conex containers, and the oxygen cylinder had been placed too close too flammable materials. A contractor working at the site, Legend Directional Services of Weatherford, Texas, has been fined $28,000 by OSHA for improper storage of flammable materials and failure to train workers in safety procedures.
As this unfortunate case illustrates, improper storage of materials can be dangerous for workers and expensive for businesses. Poor storage procedures can also introduce inefficiencies into work processes by making materials hard to locate and hampering inventory management. Here are three keys to implementing a safe, smooth, efficient storage system.
Follow Safe Storage Procedures
Safety is a paramount concern when storing materials. In order to store materials safely, four key questions should be reviewed, advises EHS Today:
- What are the physical and chemical properties of the materials being stored? Knowing this can dictate what kind of materials are safe to store together and where they can be stored safely. For example, flammable liquids should not be stored near oxidizing agents. OSHA publishes regulatory guidelines to help businesses handle materials safely.
- Why are materials being stored? For instance, materials that are only needed for just-in-time inventory can be stored in smaller quantities or for shorter periods of time, reducing potential risk.
- Where are materials being stored? For example, materials stored in containers on pallets can present special stacking risks, which can be avoided by following OSHA procedures for safe stacking.
- Where are materials being stored? Some physical and chemical environments are not suitable for certain materials. For instance, o-rings need to be stored so that they do not stretch or crack, which means they should not be stored at temperatures higher than 86 degrees F or in average relative humidity outside the range of 40 to 70 percent. They should also not be exposed to ultraviolet light or electrical arcs from sources such as motors. Consult OSHA guidelines and manufacturer instructions for proper storage procedures for specific materials.
Use Smart Warehouse Management Strategies
Managing warehouse space is another important aspect of materials storage. Once your warehouse is more than 85 percent full, you lack adequate space for new arrivals, and you begin to lose efficiency, says warehouse picking system provider Raymond Handling Concepts Corporation. If your pallets are piling up in the aisle or blocking your shipping and receiving area, you need a better storage system.
One strategy to save space is to avoid overstocking quantities of the same SKU item. This problem often happens if your purchasing agent makes a bulk sale purchase, which can result in many months’ worth of items piling up at once. See if you can arrange to have items shipped in stages or on demand to avoid using up warehouse space. Similarly, try to get rid of SKU items that haven’t turned over for a year by returning them, selling them at a fire sale discount or scrapping them.
Another strategy is using geometry to your advantage. Decreasing aisle width, making better use of vertical space, or using pallets with more storage capacity can enable you to stock more items in a smaller space.
Automate Warehouse Inventory Management
Another critical component of effective materials management is keeping up with inventory. This includes staying on top of inventory order needs and shipping schedules, as well as maintaining accurate inventory counts for bookkeeping and tax purposes.
The best way to optimize your inventory handling is to automate the process by using warehouse management system (WMS) software. WMS software system can automatically update your inventory counts as materials are received, put away and picked, reducing your need to rely on manual stock counts. You can also receive automatic notifications when supplies are running low, and even have restocking orders placed automatically.
For large warehouse needs, today’s most advanced WMS technology integrates with voice-control interfaces that let workers verbally describe the item they’re looking for in order to receive guided directions on how to locate the item’s location in the warehouse. Some companies are even starting to use warehouse picking robots to help workers physically pick items, improving efficiency while reducing safety risks.
Smart storage procedures can help you avoid safety hazards, locate materials more easily and handle your inventory more efficiently. By following safe storage procedures, using strategic warehousing strategies and automating your warehouse management, you can protect your workers, optimize your storage space, and reduce your inventory bookkeeping burden.
6078 Views