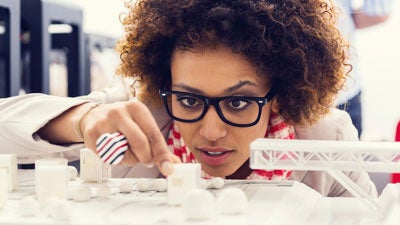
Being an owner of a manufacturing business means that your revenue, output, and client satisfaction rely on having efficient operations. But, what exactly does it mean to improve manufacturing productivity? Here’s everything you need to know! We’ve narrowed the list down to the top 9 ways to improve productivity in manufacturing.
Review your workflow
The ideal way to start is by specifying what areas of your workflow are lacking. Going over the processes in your company means considering several things, including the employees, the hardware they use, but also the physical activity of production. You’ll want to consider other factors too, such as the level of communication, the variety of resources necessary to complete tasks (raw materials, power, etc.), and so on.
Keep equipment working properly
Replacing manufacturing equipment can be pretty expensive, which is why maintenance should be one of your utmost concerns – particularly when it comes to manufacturing productivity. While keeping machines working at total capacity is crucial, so is making sure that employees are capable/competent operators. If your employees can’t troubleshoot for bugs and problems, and recalibrate the equipment accordingly, improving productivity in the production process will be considerably harder.
Be smart when stocking up on inventory
A manufacturing business won’t meet production demands without having a continuous resupply of material. However, determining the right amount of raw material for current order can be challenging. Underestimating will induce you to short your clients, making them to look the products elsewhere. Overestimating will cost you money in either storage or waste.
Implementing material requirements planning (MRP) concept can dramatically benefit your production. You wonder how? Let’s start with defining this term. What is an MRP system? Material requirements planning system is a planning and control system for inventory, manufacturing, and scheduling. It converts the master schedule of production into a thorough schedule so that you can buy raw materials and components.
Used mostly in production, this system is a push-type of inventory management, meaning that organizations use forecasting to find out the customer demand for products. The manufacturing business will forecast the quantity and type of products they will buy, along with the amount of materials to produce them. Then they push the products to the clients. MRP is an excellent way to decrease the stored inventory, the component shortages, the overall manufacturing cost, and, obviously, the cost to purchase.
Find and Eliminate Wastefulness
Waste occurs in many types and forms, some of which aren’t always obvious. For example, poor ventilation and inefficient heating or cooling aren’t usually visible. Additionally, waste happens in the form of unnecessary labor costs and employee mismanagement, which can significantly impact production efficiency.
Optimize your floor plan
To ensure peak workshop efficiency, you’ll want to take a close look at the design of your floor plan. Organizing tools, equipment, and materials properly will enhance manufacturing productivity and help keep the workplace a safe environment for workers to do their jobs.
Get rid of unused machinery
Having even a few pieces of machinery that you are not using could be real trouble for manufacturing productivity. It creates clutter, but also, you’re probably spending your hard-earned money on maintaining equipment that isn’t making you profit.
Train employees continuously
Using the latest tech trends is almost useless if your employees haven’t been educated on how to work with them. Since technology evolves fast, it’s essential for manufacturing productivity that you invest in constant education and training of your employees.
Encourage communication
Ensuring your employees are provided open channels to communicate their point of view will help improve productivity in production since you’ll be filled in on specific issues that you’d otherwise be unaware of. Strong communication will also strengthen your efforts to unite the staff around the business’s core objectives.
Consider Recycling
This is a simple way to improve manufacturing efficiency and cut costs. Make sure that you have a well-equipped facility, so you can quickly sort waste for recycling and reuse. Anything you can set back into the manufacturing process, whether scraps or leftovers, should be used.
Hope these tips help and you have everything you need to know so you can start the improvement of your manufacturing productivity. Good luck!
2032 Views