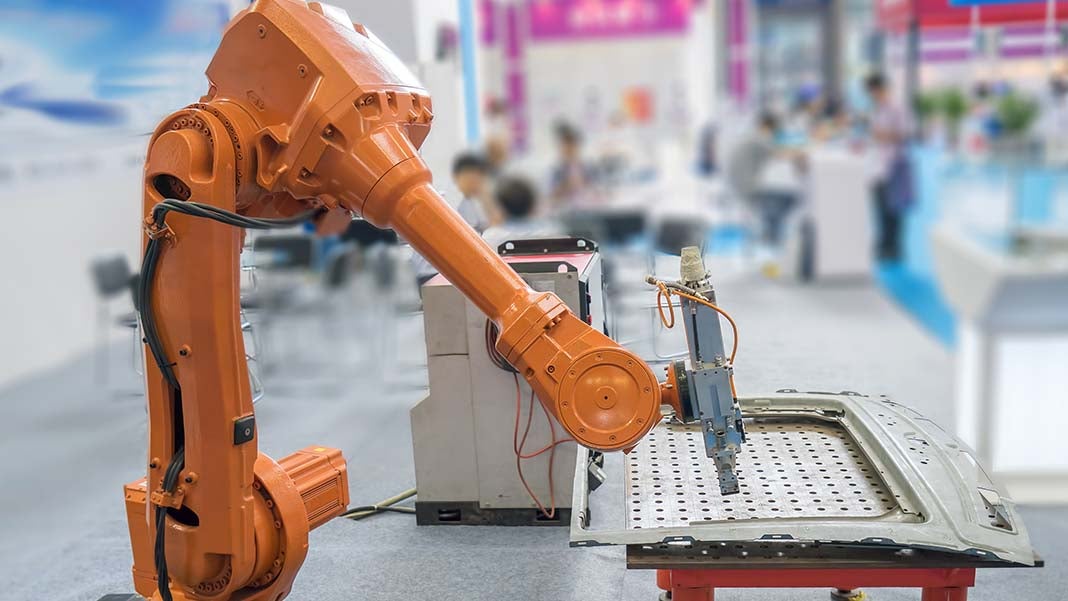
Industry 4.0 involves enhancing company processes with numerous smart technologies — ranging from robots to connected sensors. Here are specific ways that such technologies have helped the manufacturing industry progress.
Minimized Operational Downtime
Unplanned outages at manufacturing plants can result in tens of thousands of dollars or more of extra costs and lost profits. For example, a sudden equipment failure might require paying more for special-ordered parts or urgent repair visits. Relatedly, customer trust in the affected company could decline, particularly if the outage makes the organization miss deadlines.
However, many manufacturers now use smart sensors to get better visibility of single components and entire machines. Then, metrics about aspects such as vibration and temperature alert people to possible issues before outages happen. Those warnings significantly reduce unplanned outages.
Reduced Waste
The manufacturing sector popularized the lean methodology. It focuses on getting rid of waste in a plant’s processes. The lean approach raises factory output, and it can target administrative inefficiencies, too.
The lean methodology recognizes various types of waste, including:
- Inadequate utilization of an employee’s skills
- Too much time spent engaging in inefficient processes
- Poor quality control resulting in unsellable products
- Excessive investment in supplies or machinery
- Overproduction due to demand forecasting mistakes
- Non-essential movement of machines or employees
Industry 4.0 technologies tackle waste. For example, an autonomous mobile robot could restock an employee’s workstation, letting the person engage in the task at hand rather than leaving to get more supplies. Alternatively, an artificial intelligence tool could help company leaders pinpoint process bottlenecks and make adequate assessments of future demand.
Enabled Meeting Diverse Manufacturing Needs
Industries ranging from food and beverage to automotive invest in customized automated machines to improve workflows. Potential buyers can specify whether the equipment moves continuously or intermittently depending on the planned application. Automation specialists also test machines before shipping them to customers, ensuring they meet specifications.
The wider availability of customized machinery helped companies address the requirements of numerous product formats, too. In the pharmaceutical sector, for example, a company may produce items sold as pills, powders, liquids and medicinal patches. Manufacturing leaders should ideally focus on current and future goals before making equipment investments.
Improved Factory Visibility Across Teams and Locations
Cloud computing played a significant part in helping Industry 4.0 gain momentum. One advantage is that it broke down barriers that compromised smooth communications between teams. Before cloud platforms became so widespread, designers and manufacturers often did not have shared discussions about intentions for a product.
Advancements in cloud technology also help executives monitor activity and data feeds across all locations rather than just one. Suppose a leader commits to a trial of virtual reality technology across 25 of 50 factories. If productivity rises in the places that use it, such outcomes could encourage future investments.
Industry 4.0 Supports Manufacturing Success
This overview highlights why Industry 4.0 has been such a game-changer for the manufacturing sector. As more companies continue exploring smart technology’s advantages, people will notice even more benefits.
2390 Views