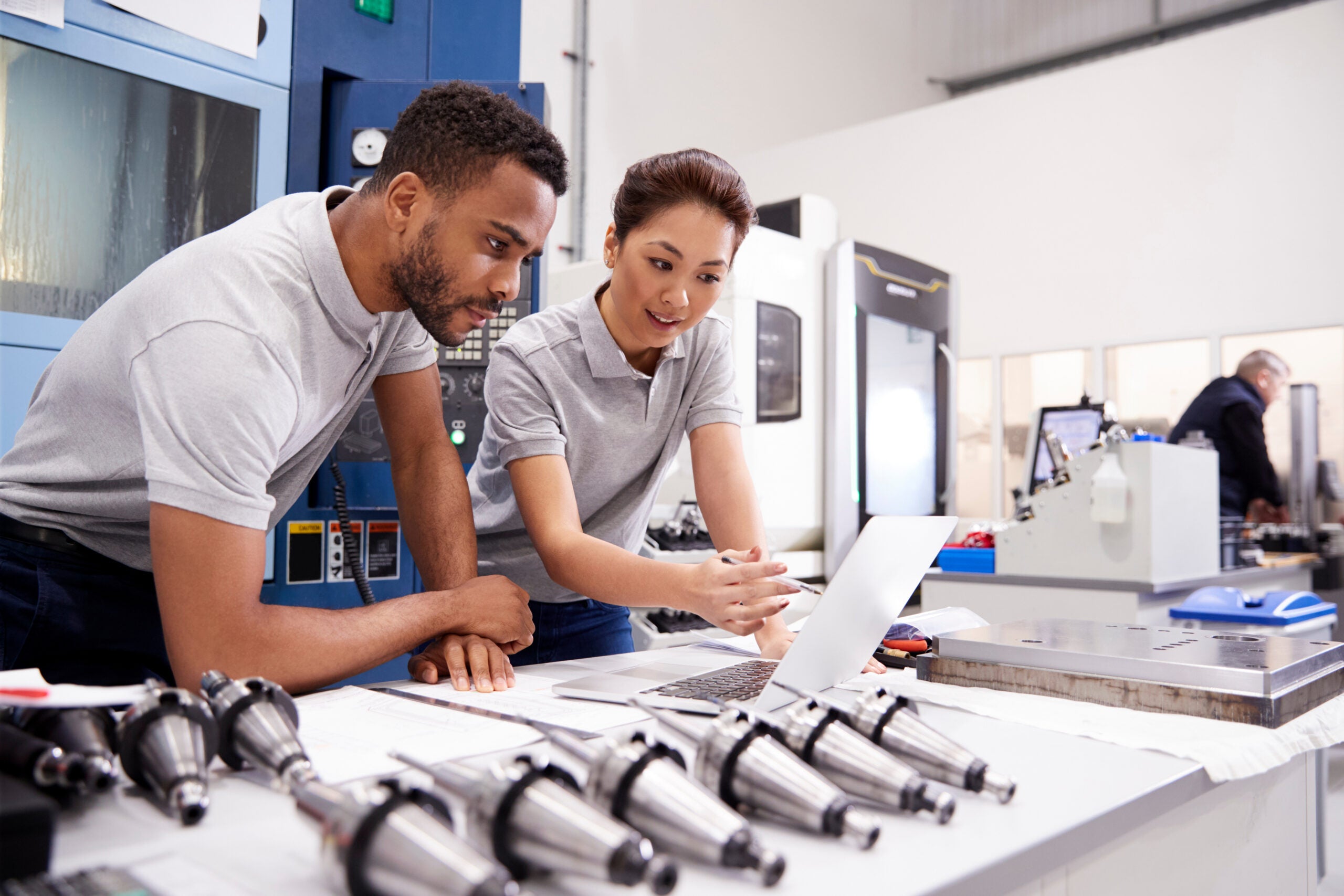
Discrete manufacturing is a sector focused on producing distinct items such as electronics, cars, appliances, and industrial machinery. Unlike process manufacturing, which produces goods in bulk (like chemicals or food), discrete manufacturing involves assembling individual units or parts into finished products. While it offers significant opportunities for businesses, discrete manufacturing comes with its own set of challenges. These challenges can impact everything from production efficiency to product quality and customer satisfaction. In this article, we’ll explore three of the most common challenges in discrete manufacturing and provide insights on how to overcome them.
1. Supply Chain Disruptions
One of the biggest challenges faced by discrete manufacturers is managing supply chain disruptions. In an industry where parts, materials, and components need to be precisely timed and delivered, disruptions in the supply chain can cause significant delays. Whether it’s due to geopolitical issues, natural disasters, or raw material shortages, a disrupted supply chain can affect production timelines, inventory management, and ultimately, customer satisfaction.
How to Overcome This Challenge:
- Diversify Suppliers: Relying on a single supplier can be risky. Discrete manufacturers should work with multiple suppliers across different regions to reduce the risk of a single point of failure. Having a backup plan in place can help mitigate disruptions.
- Leverage Technology: Modern supply chain management software can help track inventory in real-time and give manufacturers a clearer picture of where materials are coming from and when they will arrive. Predictive analytics can help anticipate delays, giving manufacturers more time to adjust their schedules.
- Establish Strong Relationships with Suppliers: Developing close relationships with suppliers and maintaining open lines of communication can help ensure faster responses in case of issues, and may even lead to priority support when disruptions occur.
2. Maintaining Product Quality
In discrete manufacturing, ensuring consistent product quality is essential to meet customer expectations and industry standards. Product defects, inconsistencies, or poor workmanship can lead to costly recalls, waste, and damaged brand reputation. This issue is particularly challenging in industries like automotive and electronics, where precision and safety are critical.
How to Overcome This Challenge:
- Invest in Quality Control Systems: Implementing rigorous quality control systems at every stage of production is key. This could involve automated inspection systems, random sampling, and standardized testing procedures. Regular checks throughout the manufacturing process can help catch defects before they reach the customer.
- Embrace Lean Manufacturing: Lean manufacturing techniques, which focus on eliminating waste and inefficiencies, can also help improve product quality. By streamlining processes and focusing on value-added activities, manufacturers can reduce the likelihood of defects caused by bottlenecks, equipment downtime, or human error.
- Employee Training: Well-trained employees are critical to maintaining high-quality standards. Regular training sessions can ensure that everyone involved in the production process understands their role in producing top-quality products and how to spot potential issues early.
3. Production Downtime and Equipment Maintenance
Another major challenge in discrete manufacturing is minimizing production downtime due to equipment failure or maintenance. Unplanned downtime not only disrupts the production schedule but also leads to lost revenue, higher operational costs, and delays in fulfilling orders. Discrete manufacturers often operate with complex machinery and equipment, making preventive maintenance a crucial component of maintaining production efficiency.
How to Overcome This Challenge:
- Implement Predictive Maintenance: Predictive maintenance uses data analytics and sensors to monitor the condition of machinery and predict when it will need maintenance. By analyzing this data, manufacturers can schedule repairs or replacements before breakdowns happen, preventing unexpected downtime.
- Regular Maintenance Schedules: In addition to predictive maintenance, establishing a regular maintenance routine for machines and equipment can help prevent issues from arising. A well-maintained machine runs more efficiently, lasts longer, and is less likely to break down.
- Invest in Training and Support: Make sure that staff are trained to handle equipment properly, troubleshoot minor issues, and understand the importance of routine maintenance. Having a dedicated support team for equipment issues can also help address problems faster, minimizing downtime.
Conclusion
Discrete manufacturing is an essential part of the global economy, providing a wide range of products across various industries. However, it comes with its own set of challenges that can affect efficiency, costs, and product quality. Supply chain disruptions, maintaining product quality, and minimizing production downtime are just a few of the hurdles manufacturers face.
By diversifying suppliers, investing in quality control systems, and embracing modern maintenance practices, manufacturers can overcome these challenges and continue to thrive in an increasingly competitive market. Staying proactive, leveraging technology, and continuously improving processes are key to maintaining long-term success in discrete manufacturing.
500 Views