Building a Sustainable Business with CNC Machining: Green Innovations in Manufacturing
By: SmallBizClub
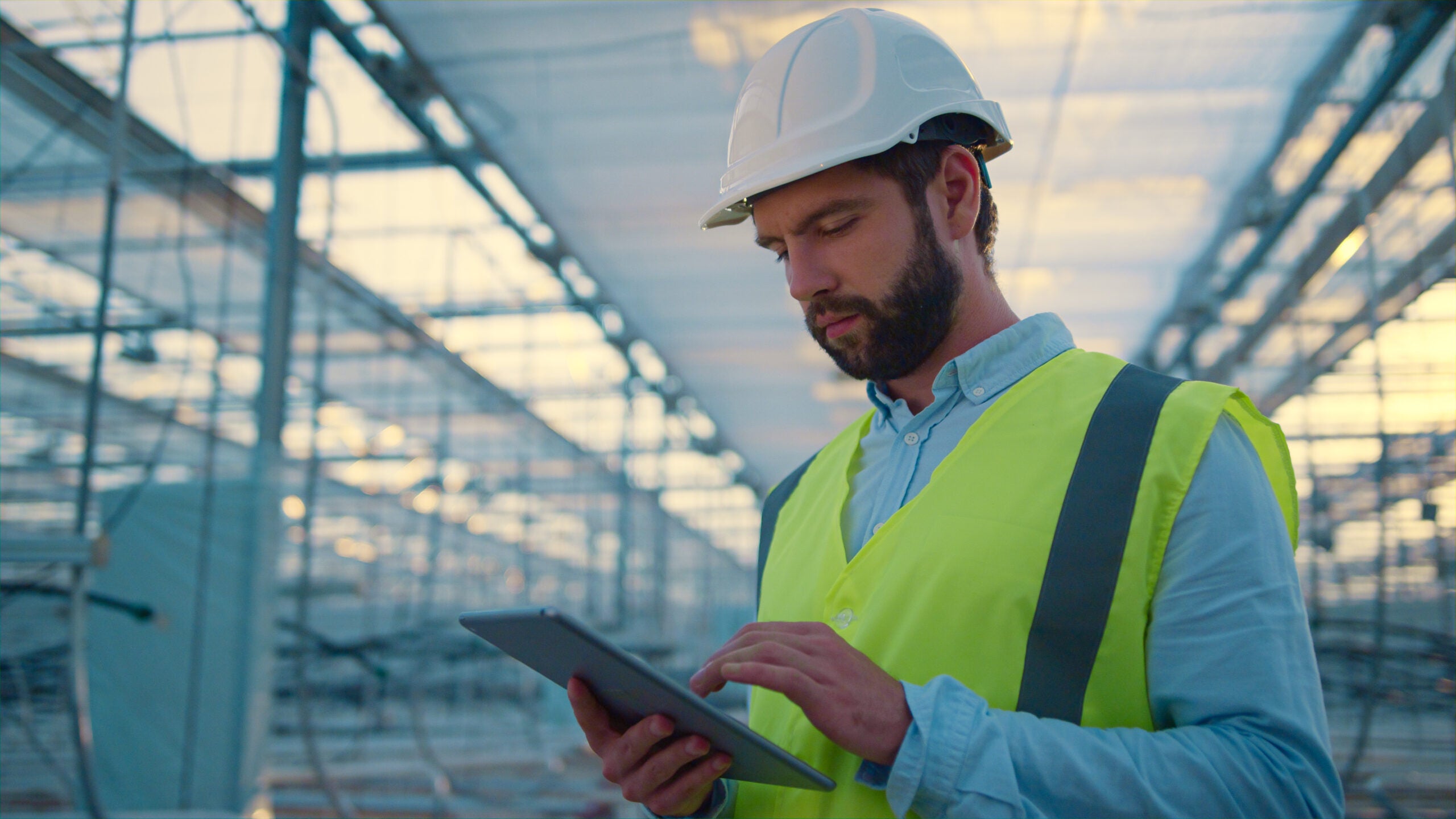
In today’s manufacturing landscape, sustainability is not just a buzzword but a crucial strategy for longevity and environmental responsibility. CNC machining, a cornerstone of modern production, faces the challenge of adapting to eco-friendly practices without compromising efficiency. This introduction explores why incorporating sustainable methods into CNC machining is not only beneficial but necessary for future-proofing the industry.
What is CNC Machining and How Can It Be Sustainable?
Computer Numerical Control (CNC) machining stands at the forefront of manufacturing technologies, known for its precision and versatility. By automating machine tools via computers executing pre-programmed sequences of machine control commands, CNC machining transforms raw materials like metal, plastic, and composites into intricate parts and components.
Sustainability in CNC machining encompasses more than just reducing waste—it involves rethinking operations from the ground up to embrace green innovations. This section delves into how businesses can integrate sustainable practices that align with economic and environmental goals.
What are the environmental impacts of traditional CNC machining?
Traditional CNC processes, while efficient, pose significant environmental challenges:
- High Energy Consumption: CNC machines require substantial power, contributing to high energy costs and carbon footprints.
- Waste Production: Offcuts and shavings from materials can accumulate, leading to considerable waste unless properly managed.
- Emission Levels: The use of certain coolants and lubricants can result in harmful emissions, impacting air quality and worker health.
How can CNC machining contribute to a sustainable manufacturing environment?
To mitigate these impacts, manufacturers can adopt several energy-efficient practices:
- Optimization of Cutting Parameters: Fine-tuning cutting speeds and feed rates to minimize energy usage without affecting quality. By adjusting these parameters precisely, CNC water jet cutters by TECHNI Waterjet can achieve optimal efficiency, reducing operational costs while maintaining exceptional precision and cut quality. This balance allows for sustainable production without sacrificing output standards.
- Recycling of Material Waste: Implementing systems to recycle metal scraps and reuse them in new production cycles.
- Upgrading to Eco-Friendly Coolants: Shifting from traditional coolants to those with lower environmental impact can significantly reduce harmful emissions.
Innovations in Green CNC Machining
The pursuit of sustainability is driving innovations in CNC machining, aimed at reducing environmental footprints and enhancing operational efficiency.
What are the latest sustainable technologies in CNC machining?
Emerging technologies that bolster green manufacturing include:
- Energy-Efficient Motors: These reduce power consumption and lower energy costs.
- Use of Recycled Materials: Integrating recycled metals and plastics in the manufacturing process supports the circular economy.
- Advanced Software for Waste Reduction: New algorithms help optimize material usage, reducing waste significantly.
Case Studies of Sustainable CNC Practices
Many companies are setting benchmarks in sustainable practices. For example, a notable European manufacturer has reduced its energy consumption by 30% through the integration of servo motors and renewable energy sources into its CNC operations. These real-life examples serve as blueprints for other businesses aiming to green their production lines.
The Role of Green Materials in CNC Machining
Sustainable materials are reshaping the manufacturing sector by providing alternatives that reduce environmental impact without sacrificing quality or durability.
What are some sustainable materials for CNC machining?
The integration of eco-friendly materials into CNC processes is vital for sustainability. Some of the prominent sustainable materials include:
- Biodegradable Plastics: These materials break down naturally and reduce long-term waste in environments.
- Recycled Metals: Utilizing scrap metal not only diminishes resource extraction but also lowers the overall carbon footprint of production.
Benefits of Using Sustainable Materials
The use of green materials brings several advantages:
- Cost Efficiency: Reduced material costs through the use of recycled inputs.
- Lower Environmental Impact: Decreased emissions and waste production enhance the company’s environmental stewardship.
- Market Appeal: Increasing consumer demand for sustainable products can lead to greater market share and customer loyalty.
Steps to Implementing Green CNC Machining in Your Business
Transitioning to a greener CNC operation requires strategic planning and commitment to sustainability goals.
How to Assess Your Current Environmental Impact
Understanding the baseline environmental impact is crucial for effective green transformation:
- Energy Audits: Identifying major energy consumers and opportunities for reduction.
- Waste Management Assessments: Evaluating waste streams to find recycling and reduction opportunities.
- Emission Analysis: Measuring the types and quantities of emissions to target for reduction.
Creating a Green Transition Plan
A step-by-step approach to adopting sustainable practices might include:
- Set Clear Sustainability Goals: Define what sustainability means for your operations—be it reducing waste, lowering energy use, or using sustainable materials.
- Invest in Technology Upgrades: Implement energy-efficient machines and eco-friendly materials.
- Train Staff on Sustainable Practices: Ensure that all employees are aware of and skilled in sustainable practices.
Challenges and Solutions in Sustainable CNC Machining
While the transition to green CNC machining presents several challenges, there are effective strategies to overcome them.
What are the financial considerations when going green?
Going green often requires initial investments which can be substantial but are usually offset by long-term savings. Considerations include:
- Upfront Costs: Higher initial costs for sustainable materials and technologies.
- ROI Calculation: Estimating the return on investment through energy savings and operational efficiencies.
Overcoming Technical and Operational Hurdles
Adapting to green technologies involves several technical challenges:
- Integration of New Technologies: Seamlessly integrating new systems with existing ones.
- Maintaining Product Quality: Ensuring that the use of recycled materials or new technologies does not compromise the quality of the final product.
The Future of Green CNC Machining
As technology advances, the future of CNC machining looks promisingly green.
What are the upcoming trends in sustainable CNC machining?
Future trends include:
- Automation and AI: Increased use of automated systems and AI to optimize energy use and material handling.
- Expansion of Renewable Energy Use: More widespread adoption of renewable energy sources within manufacturing facilities.
How can businesses stay ahead in green manufacturing practices?
Staying competitive requires continual improvement and adaptation:
- Regularly Update Technology and Practices: Keep abreast of new technologies and incorporate them as appropriate.
- Engage in Industry Partnerships: Collaborate with other companies and stakeholders to share best practices and resources.
Conclusion
Sustainable practices in CNC machining are not just environmentally beneficial—they also offer economic advantages and are increasingly demanded by consumers. The integration of green technologies and materials into CNC machining processes is essential for building a sustainable business that thrives in the competitive landscape of manufacturing.
657 Views