Lights-Out Manufacturing: Future Fantasy or Good Business?
By: Redshift
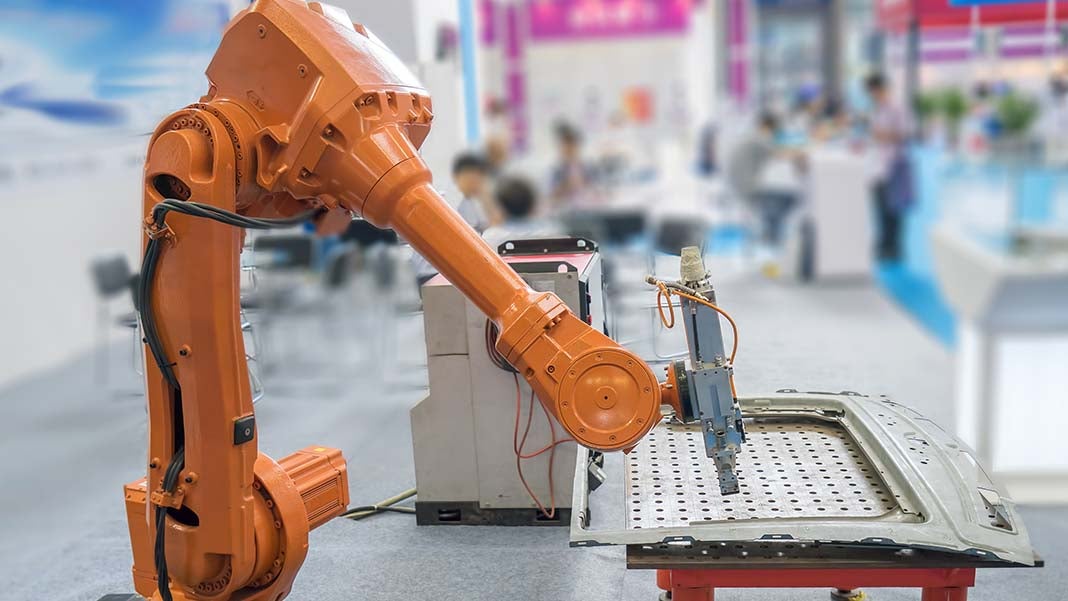
“Naturally, Man should want to stand on his own two feet … but how can he when his own machines cut the ground out from under him?”
So states the teaser for Philip K. Dick’s short story “Autofac,” first published in the November 1955 issue of Galaxy magazine. The story revolves around a post-apocalyptic world where the human survivors have lost control of self-replicating robots designed to provide them with resources. The “autofacs” become increasingly autonomous in deciding what to produce and why. The narrative follows the attempts of humans to regain control of production—possibly a forward-thinking cautionary tale?
Dystopian visions may be entertaining, but what are robots really producing on their own? Most people in the general public have an awareness that robots are being programmed to defeat humans at games like chess, poker, and Jeopardy. But if you ask most people how robots, automation systems, and lights-out manufacturing are affecting the products they buy, they probably won’t have a clue.
Lights-out manufacturing is a term that describes manufacturing operations and factories that do not need humans physically present to run properly: The factory can run “with the lights out.” Despite concerns from science-fiction authors, lights-out manufacturing operations do exist.
Probably the most well-known lights-out manufacturing facility is FANUC in Japan. At FANUC (factor automated numerical control), robots produce other robots without the presence of humans. FANUC Robotics America Vice President Gary Zywiol said about FANUC’s capabilities, “Not only is it lights out, we turn off the air conditioning and heat, too.”
The complex houses 22 factories where a huge population of honeybee-yellow robots replicate themselves 24 hours a day, seven days a week. Presently, FANUC produces between 22,000 and 23,000 CNC machines per month. With customers such as Tesla Motors and Apple and a February 2015 pledge of $1 billion to expand its operations, job stability for FANUC’s self-replicating robots is at an all-time high.
What FANUC started is becoming more commonplace in factories in the United States and abroad. But to entrust manufacturing operations to the machines, companies must first have their automation systems in place. Wisconsin-based Midwest Engineering Systems (MWES) is a provider of custom machine design and automation solutions to enable manufacturers to go lights-out. Having built thousands of automation systems since 1991, MWES knows a thing or two about the benefits, obstacles, and realities of implementing a lights-out manufacturing system.
Related Article: The Next Wave of Manufacturing Industry Trends
“Some of the advantages to implementing lights-out manufacturing are reducing and stabilizing labor costs to be reliably consistent,” says MWES Senior Sales Engineer Peter Gratschmayr. “Throughput and quality also increase. Energy requirements for HVAC control systems and lights are reduced. Scrap rates and field failures are also reduced.”
To test whether a machine is capable of continuous operation, MWES first determines whether the process capability (Cpk) exceeds 1.67. Cpk is a measure of process robustness, and 1.67 is a generally accepted measure for “four 9s” capability; that is, 99.9999 percent of parts will meet requirements, which provides a failure rate of one in a million. MWES also performs a failure mode and effects analysis (FMEA) to evaluate potential failures, as well as a flow analysis for incoming and outgoing product. If a machine passes these three steps, it’s deemed viable for continuous operation.
But even if the machines can handle the continuous workload, going lights-out may not always be the best investment. “If a client requests a lights-out manufacturing system, satisfactory criteria include determining what the relationship between the cost of the equipment versus the return of investment is in terms of labor, quality, scrap, and production-throughput predictability,” Gratschmayr says. “If this value exceeds a two-year return, the investment is less desirable.”
Even if the investment does make sense, the products may have too much variation to effectively automate 100 percent of the process. This doesn’t diminish the value of automation, however. Almost any manufacturer can benefit from automating certain steps in the manufacturing process.
The key is to identify which processes are most suitable for automation and can generate the highest return on investment. Automation is especially attractive in processes where manual interaction can result in quality or safety issues or in situations where a human worker simply can’t operate at the pace of a machine.
If an existing operation is not safe to employees, automation may be more desirable. “Robots are autonomously laser-welding nonferrous materials, performing complex force-feedback-based deburring and assembly applications, picking small components for multiple-part SKUs in place of dedicated feeder bowls at high speeds, and generally performing tasks in conditions that humans can’t physically handle,” Gratschmayr says.
So if a task is high temperature, high payload, or surrounded by toxic gases or other dangerous working environments—furnace tending, paint-line tending, glass production, or carbon-fiber cutting, for example—robots are in. Humans are out.
A common lights-out implementation, used in a machining environment, is a third-shift operation of complex parts with a multispindle machine tool. “The CNC multispindle reduces costs and work-in-process in low-volume, high-mix machining workflows,” Gratschmayr says. He also notes that the one thing manufacturers cannot do without in a machining environment is a high-quality chip-removal system.
It’s important to note that running lights-out requires complete confidence in the manufacturing process. Companies that constantly manufacture different parts don’t have the luxury of doing myriad tests to see if their operations can run lights-out. Rather, they have to rely on digital tools to create an output that can be used lights-out without first testing it physically.
Manufacturers wanting to learn more about automation should look no further than the Automate conference and exhibition in Chicago. The 2015 event, which brought in more than 18,000 attendees and 300 exhibitors from around the globe, focused on everything from modular cells, material handling, bin picking, integrated vision, coordinated motion, machine tending, and welding to collaborative-robot and soft-robot technology. With the show’s record attendance this year, it’s pretty clear that automation is in and the lights are out.