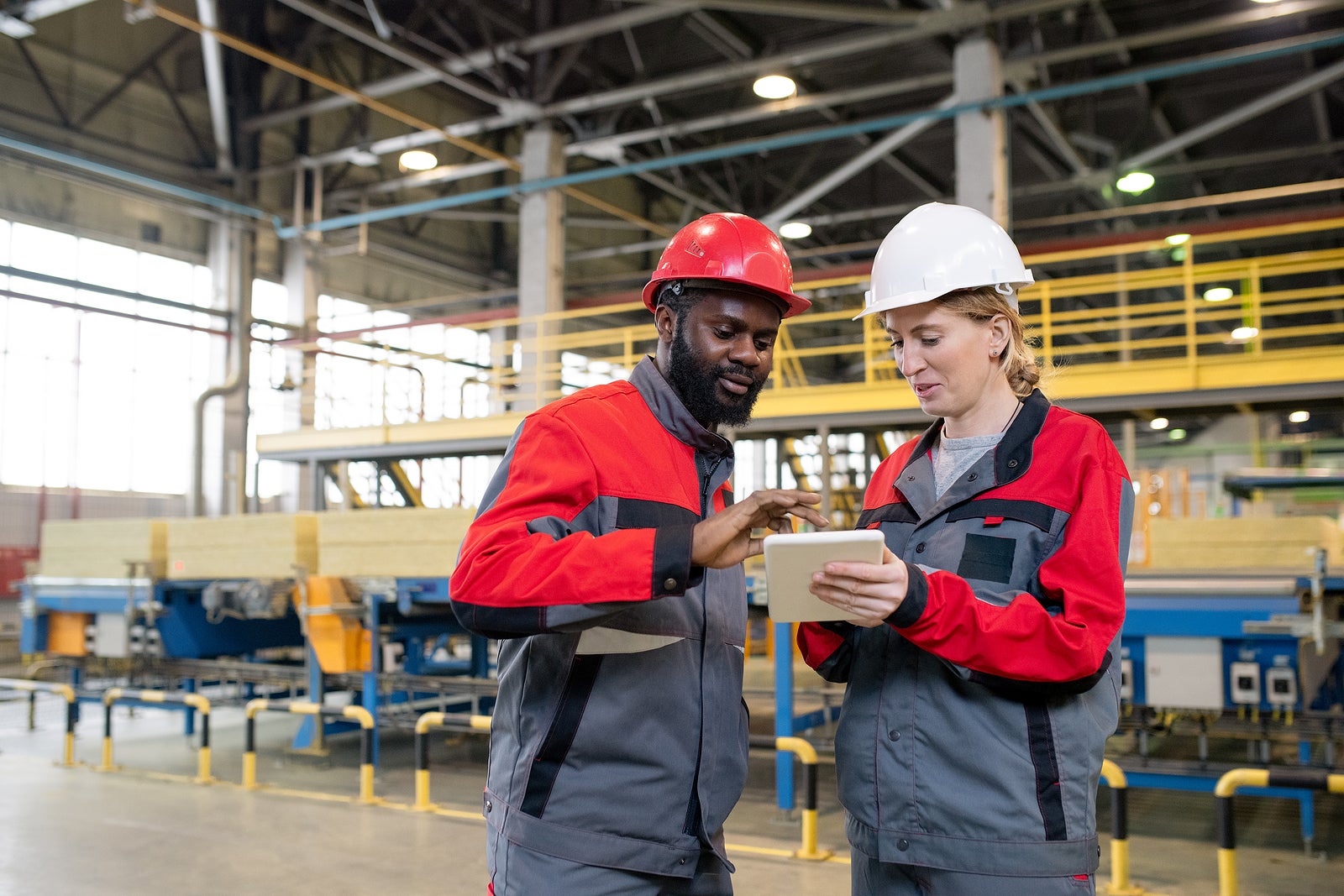
Enhancing small manufacturing facilities is an effort that can demonstrate both short- and long-term payoffs. However, it’s not always easy to decide where to start and how to get the best outcomes. Here are some practical strategies that don’t necessarily require making major financial investments.
Pinpoint and Address Communication Shortcomings
Communication breakdowns can result in some team members never receiving the most updated information. This leads to them missing out on new protocols or experiencing other challenges due to details not reaching them or coming to them incorrectly.
Andreas Eschbach is the CEO of Eschbach North America, a company that develops software for shift management. He believes the human element of person-to-person communication often gets overlooked as decision-makers review ways to improve their factories.
While commenting on the nature of the problem, he said, “I found it especially interesting in the process manufacturing industry, with its multifaceted and complex operations and units located around the globe — along with huge safety risks if important information doesn’t get to all personnel. It was obvious that this challenge can’t be solved with spreadsheets or office collaboration,” he noted.
Eschbach advocates for using an app-based solution to improve company communications. That’s not the only option, however. For example, your company might send out a monthly email or even have a group chat for people working in certain departments.
Listen to worker feedback about why they don’t receive the information in the most appropriate ways and use their input to guide company changes. For example, is the problem mainly that employees never receive information, or does it reach them too late? Perhaps the details they hear contain inaccuracies, causing them to be out of the loop.
Link Worker Training to Company Goal Achievement
Some manufacturing workers believe their companies primarily provide training to meet regulatory requirements and reduce legal risks. Those aspects come into play, of course. However, company leaders will likely have better success getting workers invested in their training by showing them how the education directly contributes to the organization’s goals.
If possible, customize the training to cover tasks the workers frequently perform rather than using more generic modules. Also, aim to make the content as interactive as possible. For example, you might shoot a short video for YouTube that shows employees how to operate a new machine. Then, use simple quiz software to check viewers’ comprehension.
Point out how training can make people more productive and confident. You could also offer more experienced workers opportunities to act as mentors to newer team members. That approach lets people share their knowledge while benefiting themselves, others, and the company at large.
Keep in mind how many of your employees — such as those working on the assembly line — probably don’t have offices they can use to complete the training. The best option may be to set up a dedicated station where people can go that’s separate from the bustle of the factory and has the equipment they need to learn.
Consider Energy-Saving Measures
Manufacturing sector leaders may believe they have little choice but to tolerate rising energy costs. However, relatively easy strategies exist for making monthly bills more manageable.
Equipment upgrades are good starting points. For example, you can combat decreased thermal efficiency by lining a boiler’s pipes with fiberglass insulation. Make sure to insulate the valves and traps, too. Doing that locks in heat, keeping energy costs down.
It’s also worth thinking about installing energy-efficient lightbulbs, especially in parts of the factory that are almost always used. Another possibility is to install sensors, so lights automatically turn off once a part of the facility remains empty for long enough. Outside of lighting, look at all energy-intensive processes and determine whether you could streamline them. For example, you might cut down on instances where machines stay running but idle.
Get to the Root of Quality Control Issues
Many manufacturing companies occasionally experience quality control shortcomings. It’s not feasible to always have error-free operations. However, the key is to address problems quickly and thoroughly. Pursuing lean manufacturing principles can help, especially since one of its goals is to achieve continuous improvement.
Data shows that problems with processes and materials cause 85% of quality deficiencies. However, when manufacturers start to track the associated trends, it becomes easier to see what’s going wrong. Perhaps it’s possible to trace 20% of complaints in the past three months back to a single supplier. A manufacturer can then engage in a frank discussion with that provider.
It’s also important to strike a balance between quality and price. For example, a supplier you’ve never worked with before may offer a drastically less expensive rate on a necessary material. In that situation, it’s tempting to give them a try. However, there’s a degree of risk when working with any new company. An alternative is to see if a trusted supplier can offer bulk discounts if you buy in larger quantities.
Let the Cloud Illuminate Changeover Opportunities
Revamping operations to allow manufacturers to navigate changeovers more efficiently can open tremendous opportunities for companies to fulfill small batches of special orders for clients. Quick changes also support producing new products to meet demand surges.
At one small manufacturing company specializing in metal products, frequent changeovers caused missed deadlines, overtime expenses and other undesirable outcomes. The organization invested in cloud technology to track shift and machine runtimes, plus changeover durations. This historical data collection played a big role since that data allowed leaders to narrow down which factors resulted in the fastest changeovers and replicate them elsewhere.
This data-driven, cloud-powered approach brought a 26% reduction in lost time from changeovers after only three months. If taking a similar approach, it’s best for factory leadership to choose and track a few metrics that’ll show if the tech investment brings the expected results.
Plant Optimization Is an Ongoing Goal
When applying these tips, remember that it’s not feasible to expect to have a fully optimized plant in a few weeks. Making this kind of progress takes time but putting continual effort into the endeavor will pay off.
2547 Views