The Promise of Manufacturing Automation for All Starts with Generative Design
By: Redshift
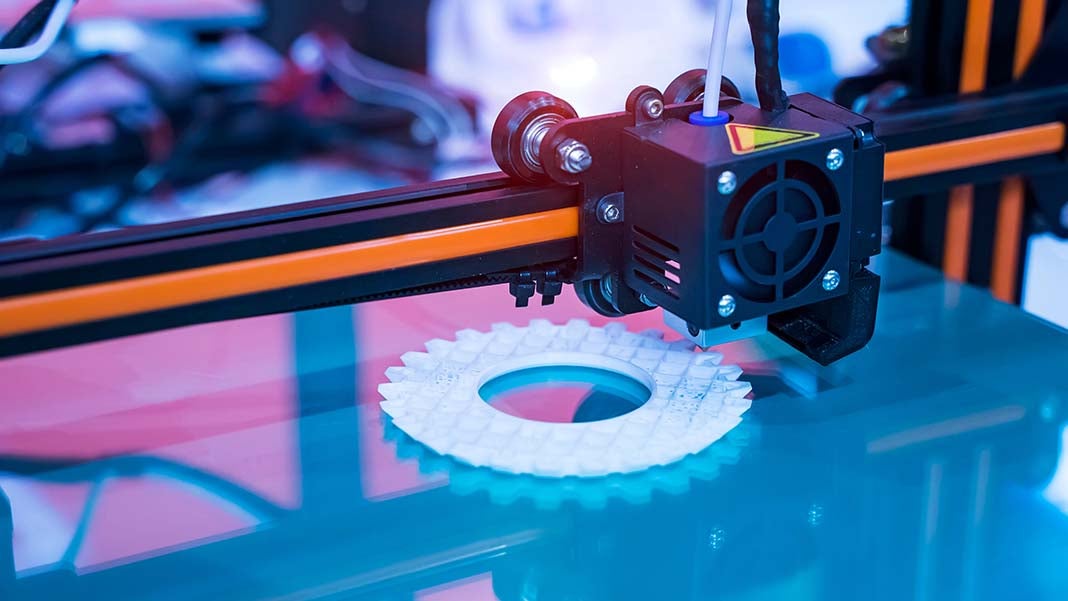
As a manufacturer, you’re certainly familiar with the concept of generative design by now—but there’s still some confusion over its real definition.
Many in the manufacturing community would have you believe that generative design is merely a branch of topology optimization or procedural modeling. But in reality, generative design is a more profound change in approach than that. It’s an artificial-intelligence-powered process that leverages the cloud to drive innovation by exploring thousands of possibilities, rather than simply removing excess material from an idea you’ve already had. (That’s topology optimization.)
If you know that, you’re hopefully already convinced of generative dsign’s revolutionary possibilities for the future of manufacturing automation. But you might also think the technology is useful solely for complex geometries that can be produced only with additive-manufacturing techniques.
To be fair, many of the generative-design examples you’ve seen to date have been intricate, often otherworldly-looking pieces printed in metal. One reason for that is because the output of generative design hasn’t been connected to the traditional means of manufacturing. And if your manufacturing business can’t afford a $2 million 3D metal printer, the technology hardly seems accessible or relevant.
Many forms of manufacturing automation are initially too expensive or too complicated to fully adopt. In the 1960s, when industrial robots first became available, only the likes of GM could afford them. Generative design—the automated process of creating a design geometry based on simulation outcomes that are generated with an understanding of the manufacturing process—is just the latest seemingly out-of-reach tech. But the good news for manufacturers is that the scope of generative-design automation is expanding to include new manufacturing processes that support traditional manufacturing.
With a manufacturing constraint such as casting or machining, generative-design software can produce results that you can fabricate using tools and equipment you likely already have in your shop. These outcomes aren’t just possible; they’re affordable.
Take, for example, three versions of a metal support part for a wheelchair, derived from the same generative-design output. Each part is essentially the same: same functional and performance requirements, same material, same rough form. The only difference is the manufacturing process, but as you’ll see, not all processes are created equal.
The original part is die-cast out of metal, at a cost of about $15 when tooling costs are fully amortized. The 3-axis-milled iteration can be made on a more common machining center, but it costs closer to $100 to make, due to the length of time it takes to machine the organic form. The third option—2.5-axis milled—is utopia because it gives you a part that does everything the die-cast part does, but for $25. For roughly the same price, you get the absolute best solution for your design problem, without the need for custom tooling, and you can make it with your existing machine-shop hardware.
Clearly, the manufacturing process is a big influence on the type of geometry you produce, and it’s finally possible for anyone to apply generative-design technology to accessible means of manufacturing. But the promise of manufacturing automation doesn’t stop with generative design.
To realize the next significant advance in automation, a digital pipeline is necessary to enable a continuous workflow from concept to physical product. Consider today’s basic product-development workflow: An engineer completes some design geometry and then hands it over to someone else to do simulations. That person has to finish the simulations and validate them before handing off to yet another person who creates the machining instructions in the form of g-code. In many cases, that g-code file is then copied onto a memory stick and walked down to the shop floor, where the machinist can load it onto the machine controller and actually start to cut metal.
That waterfall workflow is linear and highly inefficient. A better way forward is an automated, agile product-development process, one that allows for some form of concurrency so that one person can start working on simulation studies before the design is even finished. With feedback from the simulations, someone else can start the manufacturing instructions also before the whole design is complete.
This enables your business to work less like a 19th-century factory and more like a highly competitive sports team. Having process elements happen in parallel shortens the total amount of time it takes to produce a product, and it leads to greater product innovation, better product performance, lower costs, and faster time to market—all key attributes of a killer business.
To really make that work, you need to create that digital pipeline: a direct connection between the manufacturing instructions produced in the software and the machine tool. In that scenario, the g-code is created in the background and sent straight to the machine tool without the designer ever being conscious of it. Think of it like this: If you want to print something on paper, you send it over the network, directly from the word processor; you don’t copy files across the network or insert a thumb drive to make the printer understand what you typed into your word processor. The same should be true in manufacturing, with a network of machines and CAD/CAM applications.
As valuable as that type of manufacturing automation is, it’s still linear and thus incomplete—the information goes to the machine tool, but no feedback returns. Things would be more inspiring if those controllers on the machine tool could also capture information about the tool’s performance. That kind of automation would provide closed-loop feedback, allowing you to take information from the machine tool and update the machining instructions in real time.
When a CNC machine cuts metal, the spindle turns and drives the cutter into the metal. The controller knows how much pressure is on the spindle and its maximum capacity. It knows, for instance, if the spindle’s under 50% of its maximum loading condition in the middle of an operation—which means it has 50% capacity that you’re not leveraging.
With a direct networked connection to the machine controller, you can “listen” to the controller and, in real time, update the machining strategy that you’ve automatically generated in your design software. If you’re aware that the spindle load capacity is at 50%, you can either increase the feed rate so that the cutter goes through the material faster or cut deeper to remove more material. Either choice increases the spindle force, pushing the machine further toward its limit. And that means you can manufacture faster and get better operational efficiency at the factory.
Taken all together, these three forms of manufacturing automation—generative design, digital pipeline, and closed-loop feedback—present a powerful case for a new way of working. Today, you can input traditional manufacturing constraints into Autodesk Fusion 360 and use its generative-design functionality to produce optimal design solutions. Soon, the digital pipeline and ability to reclaim information through connectivity to the shop floor will no doubt change your business outcomes for the better. For manufacturers, the best really is yet to come.