5 Ways the Modern Assembly Line Moved to Automation and Back to Humanization
By: Redshift
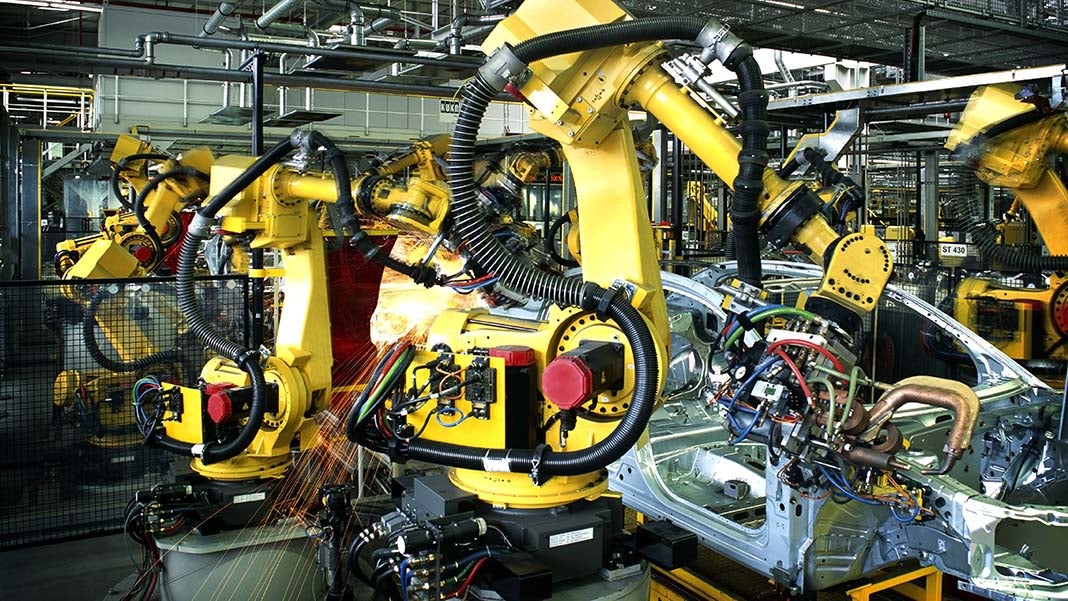
Since the debut of the modern assembly line on at the Ford Plant in Highland Park, Michigan on December 1, 1913, manufacturers have continually experimented with improving its promise of speed, efficiency, and reliability. Far from a static technology, the assembly line invites change: Automation via robotics, new factory designs that lower manufacturing’s environmental impact, and software optimized efficiency have all revolutionized the assembly line. This look at some of the latest innovations and the assembly line’s past shows how factory automation improved workers’ lives, found a limit to automation, and may find balance in human/machine collaboration.
1. Can Lines Engineering Streamlines Conveyor Systems
Next time you crack open an ice-cold beer, take a moment to consider the machinery that helped put that brew into your hand: the conveyor system. Family-owned Can Lines Engineering, which designs and manufactures conveyors for Anheuser-Busch, Coca-Cola, and others, understands the important role this technology plays in keeping America’s coolers stocked with frosty beverages. The company constantly looks to streamline its own production to create better designs and meet client demands.
2. What Can the Assembly Line Teach Us About Innovation?
It’s been more than a century since Henry Ford’s assembly line catapulted his company into market dominance, thus transforming the entire manufacturing sector. While many of the assembly line’s production methods had been previously used, Ford synthesized those concepts and established some keys to future innovation: comfort with uncertainty, a willingness to experiment (and fail), and giving brilliant minds free rein to create.
3. Mo Rocca: The Henry Ford’s Innovation Nation Model T
Shortly before launching his company’s signature vehicle, Ford explained to his sales team, “Any customer can have a car painted any color that he wants, so long as it is black.” Ford understood that in order for the assembly line concept to work, variations needed to be minimized. While that fomented pushback from some in the company, Ford’s insistence on simplicity resulted in a 93-minute assembly time for the Model Ts, despite its 10,000 parts. That efficiency also led to the 40-hour workweek (as well as higher pay), which vastly improved workers’ lives.
4. Tesla Is Temporarily Shutting Down Model 3 Production. Again.
While Elon Musk’s SpaceX has been busy launching rockets and even transporting cars into orbit, back on earth Tesla’s Model 3 production has run into the limitations of automation. The company shut down manufacturing for several days after falling behind production goals, which were attributed to “excessive automation.” As Musk admitted on Twitter, “Humans are underrated.”
5. Continued Evolution of the Toyota Assembly Line
Eight years ago, Toyota unveiled its flexible assembly line, which the company continues to tweak to reduce investment costs in new lines by its goal of 40 percent. By removing much of the overhead structures and focusing on human/robot collaboration—among other changes—the company aims to build smaller plants with reduced carbon footprints and greater flexibility and efficiency. The result? Toyota’s Tsutsumi Plant in Japan produces Camrys cheaper than its facility in Georgetown, Kentucky, despite higher labor costs and having to ship the vehicles across the Pacific Ocean.